Regenerative Thermal Oxidizer Treating Medical Product Coating Emissions
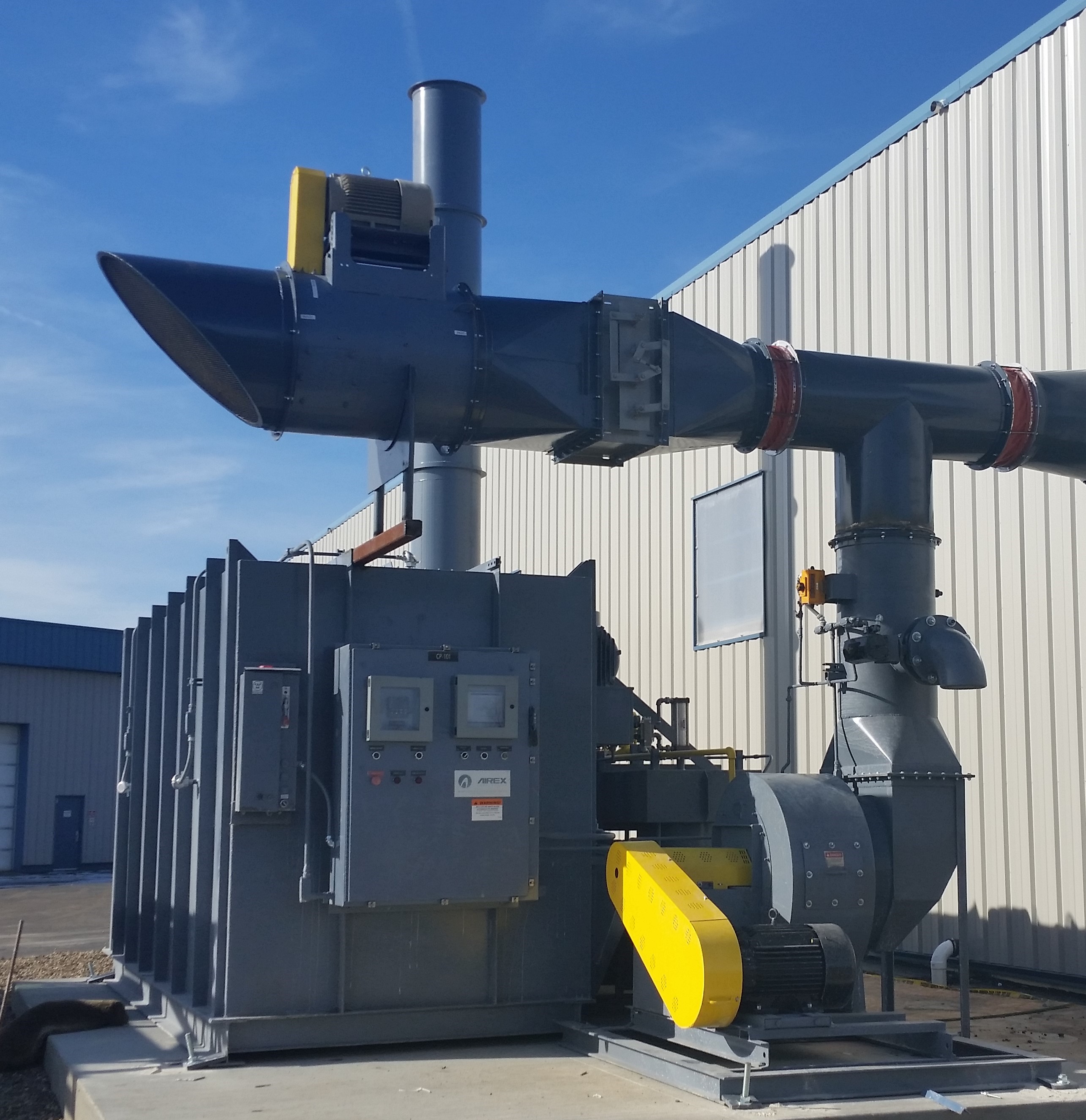
A manufacturer of medical spiral cores/straws needed to economically control emissions. We provided a very economical system with low operating costs.
Problem
A manufacturer of medical spiral cores/straws needed to economically control emissions. Their growth had resulted in increased emission tonnage, and they were nearing the limit without a control device. Their emission stream consisted of simple hydrocarbons with no particulate or halogens in the airstream. Like many manufacturers, they had planned for a control device, but as the time of decision approached they could not accept the cost of a new system
Photos: In Progess
Click on a picture to enlarge
Solution
Kono Kogs had a system that was very economical for them, and very low cost to operate. For less than half the cost of new equipment, we provided a fully refurbished RTO with both a VOC destruction warranty and parts warranty.
Kono Kogs also provided turnkey installation and a ductwork capture system. The customer had multiple winding machine hoods that required capture. This required multiple ductwork drops from a main header hung from the ceiling of the plant. The process of the RTO installation including the ductwork took only 10 days.
Once installed the equipment started up in just a few days. The time it takes from the decision to purchase the equipment to it being in operation can be very short when you choose used equipment from Kono Kogs. The time commitment is much shorter than waiting for an OEM to manufacture new equipment. This can be an advantage for customers requiring short turnarounds.
Photos: After
Click on a picture to enlarge
Equipment & Services Provided
- Fully refurbished used Regenerative Thermal Oxidizer (RTO)
- Performance and parts warranty
- Low-cost RTO at approximately half the cost of their new equipment options.
- RTO provided had been idle for 10 years so it needed extreme refurbishing & component replacement due to long-idle components; many simply replaced
- Upgraded operator interface to a touchscreen & added a remote screen as well.
- Added bypass functionality with bypass t-damper, logic and bypass fan
- Oxidizer PLC logic modified to interface with customer process
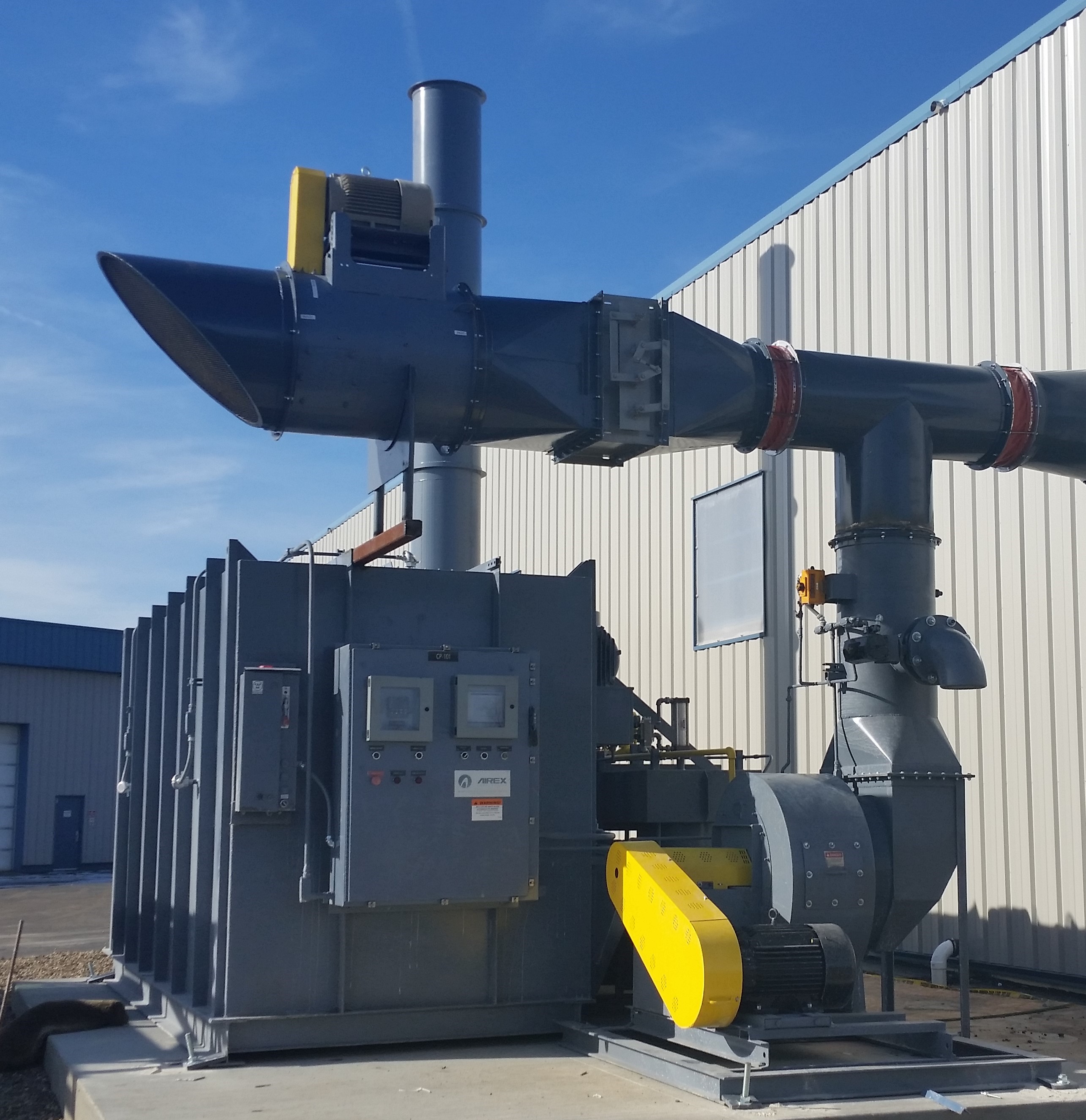
Results
RTO met or exceeded all customer demands for this project at 60% of the cost for a new system. This system was well built just needing most of its mechanical parts replaced due to non-use. The result was a low cost, reliable, refurbished regenerative thermal oxidizer.