Treating Metal Decorating Emissions with a Dual Regenerative Thermal Oxidizer
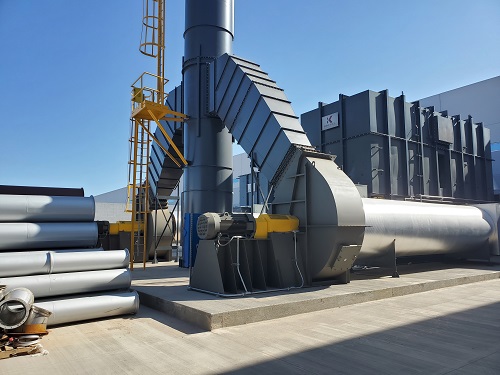
See how Kono Kogs helped this company meet their air pollution control regulations with a turnkey solution that included a refurbished RTO.
Problem
This metal decorating (can coating) application has highly condensable volatile organic compounds (VOC), which tend to build up on the fan wheel in a typical forced-draft RTO system. This causes fan imbalances and requires housekeeping to keep the wheel clean.
This application has both cold (inside spray) and hot (inside bake oven & pin oven) airstreams that combine just prior to the RTO.
Challenge #1: VOC condensation buildup
This can coating application has highly condensable volatile organic compounds (VOC), which tend to build up on the fan wheel in a typical forced-draft RTO system. This causes fan imbalances and requires housekeeping to keep the wheel clean.
Challenge #2: Two airstream temperatures
This application has both cold (inside spray) and hot (inside bake oven & pin oven) airstreams that combine just prior to the RTO.
Challenge #3: Industrial NOx emissions
Nitrogen oxide (NOx) emissions are poisonous and highly reactive, and many regions have adopted regulations requiring reduced NOx emissions from industrial facilities.
Challenge #4: Protecting equipment and productivity
Preventive regenerative thermal oxidizer maintenance is essential. Because RTOs are exposed to harsh chemicals and high temperatures, small problems can quickly escalate to major issues without following a consistent maintenance plan. Our customer needed to keep up routine maintenance while minimizing operational downtime.
Solution
Solution #1: Relocate RTO Fan
The solution was to move the fan to the exhaust side of the RTO where the higher temperature on the outlet of the RTO prevents build up on the fan and fan wheel.
Solution #2: Install inlet Mixing Box
Kono Kogs added an inlet mixing box before the two RTOs to control air temperature entering the RTO. This prevents condensate buildup on duct walls and the RTO valve.
Solution #3: Gas train overhaul, natural gas injection
Natural gas injection was added, which provides exceptionally low operating costs and low NOx conditions. Kono Kogs also added a low NOx burner so the client would meet local codes.
We also completely overhauled the gas train and performed needed upgrades for proper control of the new low NOx burner.
Solution #4: Tandem RTO Arrangement
For process operating flexibility, an innovative tandem operation was provided by adding:
- Priority logic
- Additional isolation dampers for each RTO
- A common ductwork header design
The result is all eight processes exhausting to this tandem RTO arrangement can be directed to either RTO or both RTOs, facilitating routine maintenance. The tandem RTOs share one common 60-ft. exhaust stack with an OSHA approved access platform, including handrails and continuous tie-off system up the side of the access ladder.
Kono Kogs also added a fully redesigned and UL-rated control room featuring an Allen Bradley ControlLogix PLC (programmable logic controller) and PanelView HMI (human-machine interface).
Equipment & Services Provided
- Turnkey installation of two refurbished RTO systems
- Mechanical assembly of both systems
- Ductwork
- Process dampers
- Electrical wiring
- Natural gas & compressed air tie-in
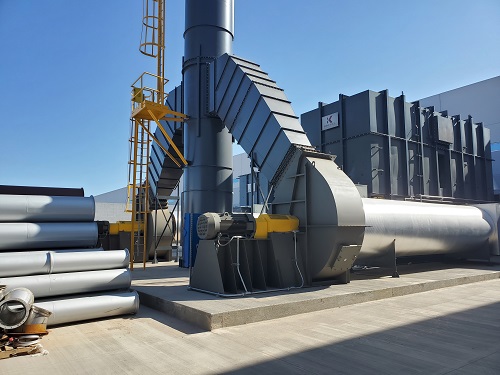
Before & After: Two Turnkey Refurbished RTO Systems Installed by Kono Kogs
Starting with the right RTO design
The process started with two well-built systems from our used RTO inventory featuring one of the best rotary valve designs on the market. Rotary valves significantly reduce pressure spikes caused by valve switches back to the process, which was important for this manufacturing process (and any other pressure-sensitive application).
Extensive RTO Refurbishments
In addition to the application-specific updates detailed above, Kono Kogs also performed the extensive refurbishing we are known for.
The RTOs were stripped down to their main components: the rotary valve, ceramic media chamber and combustion chamber. Kono Kogs provided new ceramic media designed specifically for this application, to mitigate plugging.
Nearly all auxiliary components, including the fans, blowers, exhaust stacks, burners, and most of the gas train were replaced.
On the remaining sub-systems, Kono Kogs:
- Refurbished the rotary valves (including new seals)
- Fully rebuilt the air cylinders
- Replaced the solenoid actuating valves
- Inspected and repaired any cold face issues, combustion chamber & media bed insulation
- Tested and replaced all instrumentation as needed
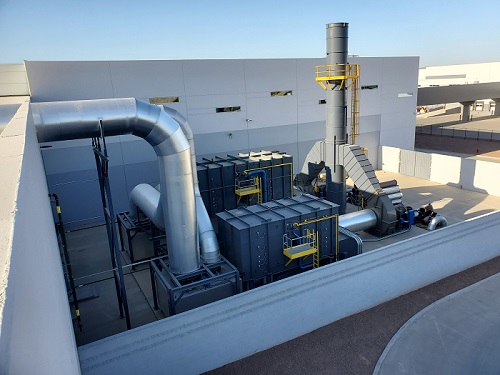