.avif)
What is KONOConnect?
KONOConnect is a cutting-edge remote monitoring system that securely tracks and records critical parameters of your oxidizer system using Industrial Internet of Things (IIoT) technology.
- See real time performance on your device with our user-friendly interface.
- Maximize oxidizer uptime with alarms, fault warnings, and out-of-parameter notifications sent your team and ours.
- Make predictive maintenance decisions with on-going data storage and trending.
Exceptional cybersecurity through our partner, ei3.
Real-Time Metrics for your RTO System
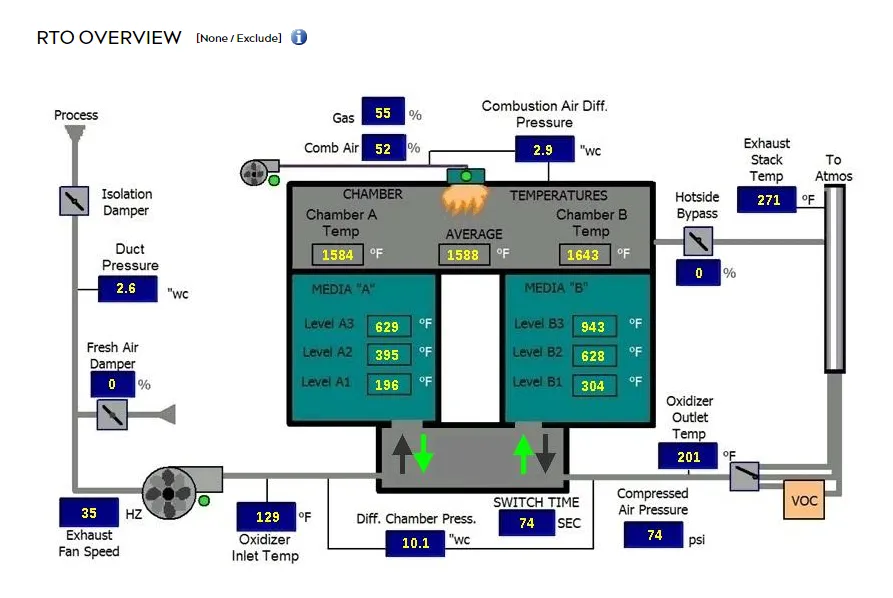
Key Features & Benefits
Minimize Downtime with Proactive Maintenance
The real-time data captured by KONOConnect allows you to identify potential issues before they escalate into major problems. This proactive approach to maintenance means you can address issues promptly, preventing costly downtime.
Optimized Performance
KONOConnect's ability to monitor, record, and trend key parameters such as temperature, pressure, fan/motor speeds, and burner firing rates can help ensure your RTO equipment is always operating at peak performance. Trend analysis with such an abundance of critical data allows our team to optimize the RTO to its full potential, lowers utility use, and significantly expedites troubleshooting.
Data-Driven Decisions
The historical data analysis feature of the KONOConnect system allows you to identify trends and patterns over time. By leveraging the power of the ei3 remote monitoring system, you're not just reacting to issues - you're anticipating them.
What KONOConnect provides:
.avif)
.avif)
.avif)
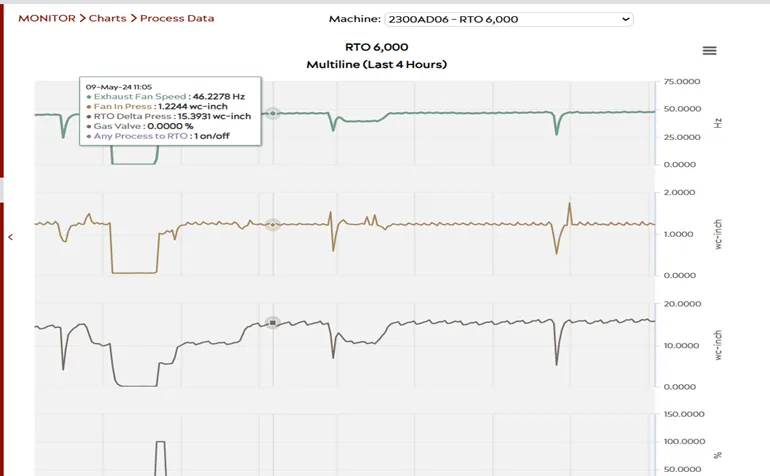
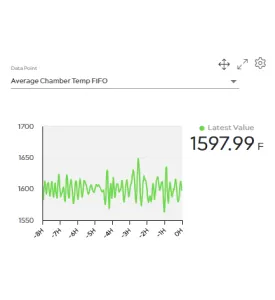
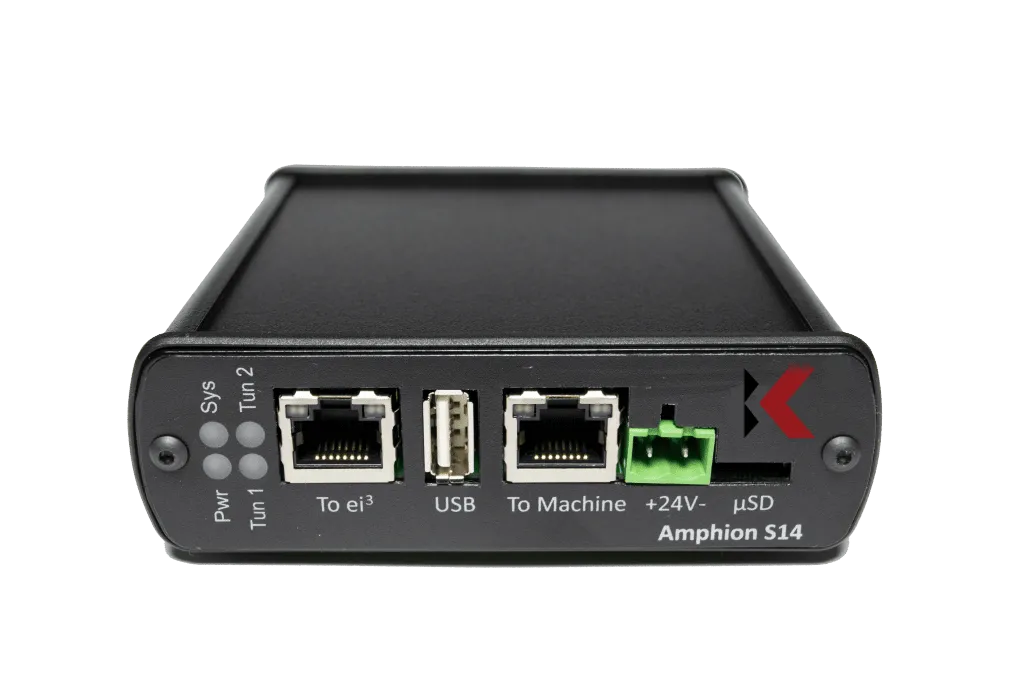
KONOConnect Levels
Service Application
- Remote Troubleshooting
- Communication Router
Data Collection
- Remote Monitoring
- Remote Troubleshooting
- Downtime Tracking
- Lifecycle Maintenance Tracking
- Monthly EPA Reports
- Communication Router
Expert Level Security
KONOConnect operates on ei3's secure system. ei3 places the utmost importance on data security and privacy, offering a comprehensive and secure solution for industrial IoT. Read more about ei3's cybersecurity measures.
Managed Secure Network
ei3 ensures oversight of network connection points, enabling secure, encrypted outbound connections for equipment.
End-to-End Data Protection
ei3 ensures data security across all stages—from machines to cloud, end-user apps, and backend system integration by linking machines to ei3’s private cloud.
Private Dedicated Servers
ei3's private servers, in your chosen location, ensure 24/7 availability, backup, and unlimited data storage for machine data.
Purchase KONOConnect as a stand-alone service or Bundle It with our KONOCare preventive maintenance packages for highest oxidizer performance and reliability.
Request Service Form
Please fill the form below to receive a service quote. You can also call us 24/7/365 at 920-461-9078 or send us an email.