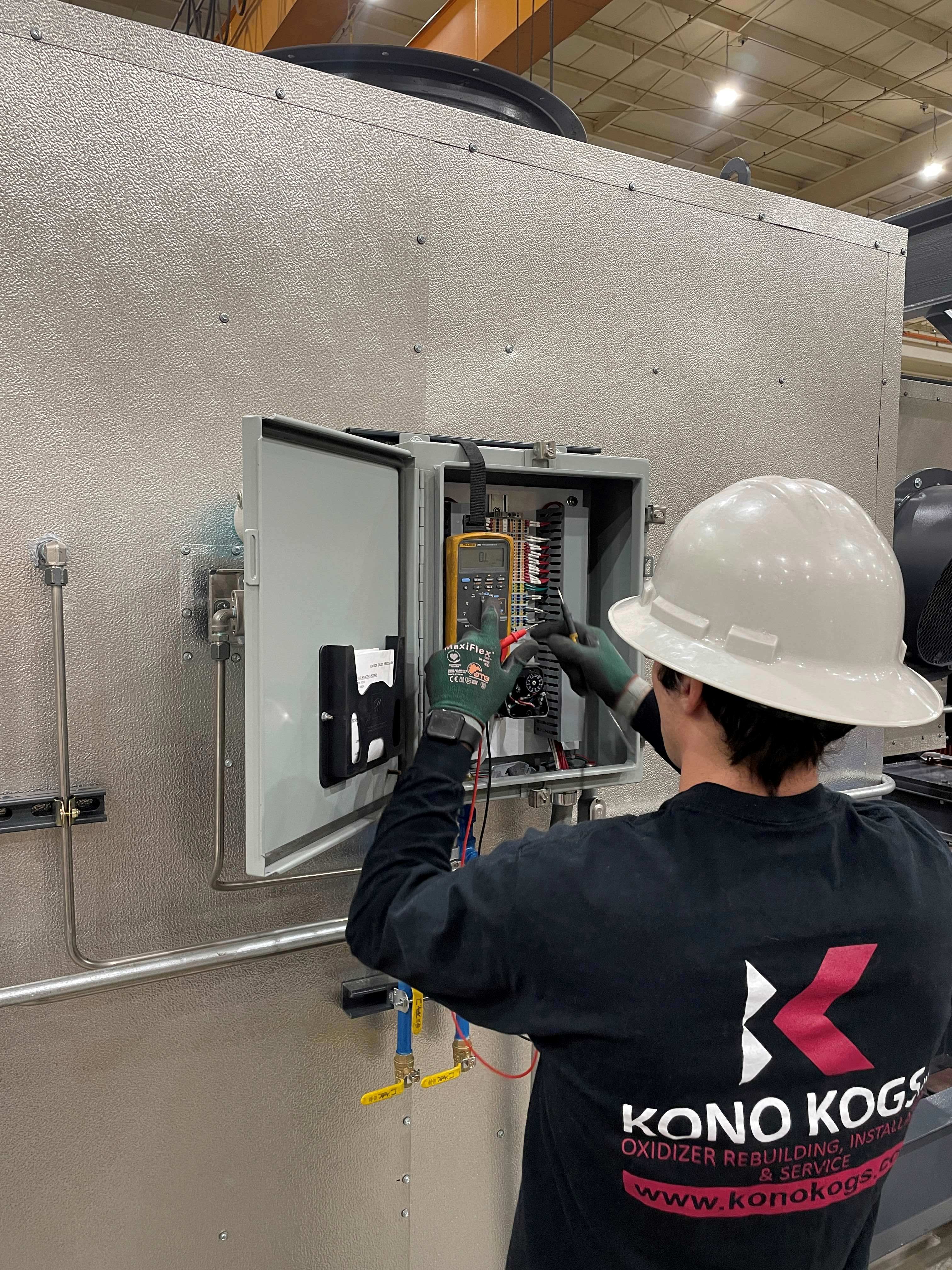
What is KONOCare?
Kono Kogs will create a custom KONOCare RTO preventive maintenance program for your plant and equipment, regardless of oxidizer OEM. Over our 25+ year history we’ve worked with virtually all makes and models, and our core team has 150+ years of combined application and technical experience.
Maintenance Programs Optimized for YOUR Specific Needs
KONOCare preventive maintenance (PM) plans have been developed with the help of our Fortune 500 customers. The goal: maximum oxidizer uptime. Starting with a goal of zero non-scheduled downtime, we set out to define the most practical path to that goal.
The number one cause of oxidizer lost time is part failure. Identifying at-risk parts or deteriorating oxidizer health well before they impact performance or up-time is what drives our KONOCare PM plans. These plans also point to the importance of collaboration between Kono Kogs and our customers in this effort. Equipping, training and communicating with your in-house maintenance team will lead to the success we each desire.
We offer 4 plan levels to meet your uptime goals
KONOCare Plan Options
Silver is the most popular plan among our clients. However, it’s not the answer for every facility, or every emission airstream. Difficult applications or stringent emission regulations will require more diligent and frequent PM to keep your oxidizer running efficiently and your facility in compliance.
Select a KONOCare plan option below to learn more about what it includes:
KONOCare Diamond
Our top-of-the-line offering.
Well received by our largest customers.
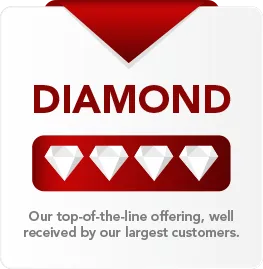
2 Customized for each system to meet your needs
The Diamond level PM plan is our top-of-the-line offering and has been well received by our largest customers and plants with no ability to produce goods without a functioning oxidizer.
KONOCare Diamond includes:
#1: Extensive spare parts package covering:
- Critical level
- Secondary level
- “What if” level
#2: Remote monitoring hardware/setup (if not already installed)
#3: Extensive onsite training for plant leadership & maintenance personnel
- In-class training
- Principles of oxidizer operation
- Control loop review
- Importance of record keeping
- On-machine training
- Component identification
- Terminology
- Identify data point locations for record keeping
#4: Highest level of system remote monitoring - 24/7/365 monitoring and data logging; with option for additional billed support
- Minimize your downtime with proactive maintenance
- Optimize your RTO's performance
- Make data-driven decisions with historical data analysis
#5: Monthly maintenance reminders by e-mail
#6: Extensive training of plant & maintenance personnel during initial PM visit
- Review operation & maintenance requirements with plant personnel
- Review recordkeeping requirements: visual, pressures, temperatures, amperages
- Discuss KONOCare maintenance reports and what to expect in the reports
#7: Quarterly onsite PM inspections
- Review the following with plant personnel:
- Past KONOCare maintenance reports and any open items
- Service calls since previous PM visit
- Alarms since previous PM visit
- Parameter sheets (stressing the importance of recordkeeping)
- Trends seen in parameter records and their meaning
#8: Monthly report drawn from remote monitoring data
- Relevant graphs of critical parameters (pressure, temperature, amperage) with technical insights from Kono Kogs Team
- Report on observable trends in parameters
- Identify at-risk parts and oxidizer health risks
Why our largest clients love KONOCare Diamond: The combination of trained eyes on the equipment both quarterly and remotely, plus trained and engaged onsite maintenance personnel, will ensure the oxidizer system can be relied on in both the short and long term.
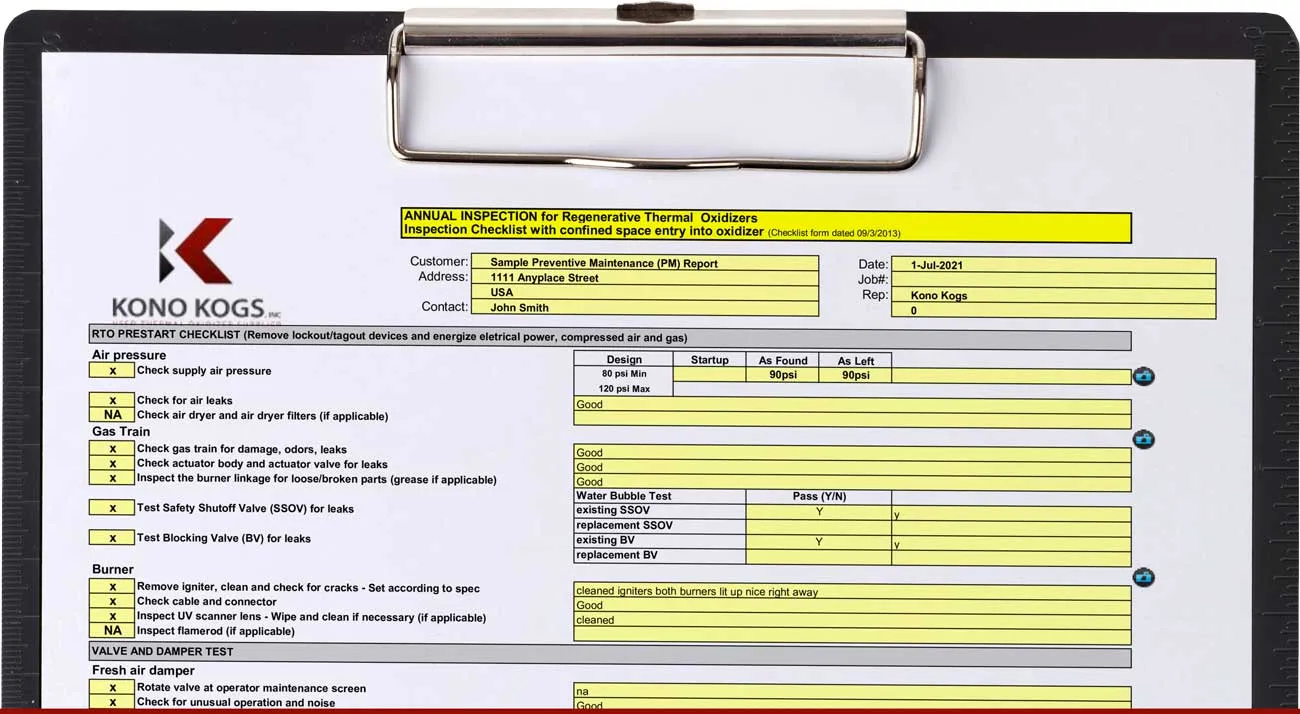
All KONOCare plans include at least one annual onsite preventive maintenance visit.
Typically, preventive maintenance service takes place over two days. The air pollution control system will need to be shut down (and cooled) before our technician begins, and remain shut down for the first day of preventive maintenance. This involves a complete internal and external mechanical inspection, including consumable component replacement. On the 2nd day the system will be on and off as we perform operational testing.
Day 1 includes mechanical inspection of:
- Combustion chamber
- Compressed air piping
- Gas train
- Dampers
- Poppet/Rotary valves
- Ceramic media
- Catalyst
- Insulation
- Fans
- Ductwork
- Exhaust stack
- Burner(s)
- Expansion joint(s)
- Control panels
- Plenums
- Flame safeguard unit
- Cold face
- External hot spots
Kono Kogs maintains a large inventory of replacement oxidizer parts. We also have our own fab shop and can produce custom components if necessary. Even more importantly, our team has the skills and knowledge to keep your process running reliably at peak efficiency.
Day 2:
The second day involves performance evaluation, including a complete review of system operation in on-line and off-line modes, electrical inspection and component testing. On day two the system will be started up and shut down to conduct process control and operational analysis.
Day 2 evaluation and testing includes but isn’t limited to:
- System startup cycle
- Online conditions
- Safety shutdown
- Alarms
- Valve cycling
- Pressure control loops
- Temperature profile
- Pressure/temperature controls
- Relays
- Test all safety switches/logic
- Burner tuning
- Burner controls
- Airflow switches
- Internal hot spot inspection/repair
- Thermocouples (replace TCs in combustion chamber)
- Actuators
- Motors
- Variable frequency drive (VFD)
- HMI & communication devices
- Data recorder
After each preventive maintenance visit you’ll get a detailed report including:
- Full checklist of system components & operations reviewed on site
- Work completed by technician
- Results of testing
- Critical findings requiring action
- Photo record of all areas, especially critical areas
- Recommended monthly maintenance plan
To better understand the level of inspection and detail covered during a preventive maintenance visit by Kono Kogs, view or download our RTO inspection sample report PDF:
KONOCare Platinum
Everything offered in Gold
+ plus very high-end support, oversight and reporting
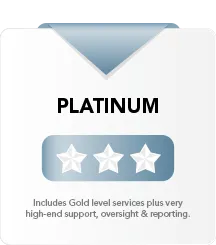
2 Customized for each system to meet your needs
KONOCare Platinum and KONOCare Gold include services that fall between Diamond (above) and Silver (below). Each KONOCare plan is optimized to suit your needs.
Share your application with us for a custom recommendation and quote.
All KONOCare plans include at least one annual onsite preventive maintenance visit.
Typically, preventive maintenance service takes place over two days. The air pollution control system will need to be shut down (and cooled) before our technician begins, and remain shut down for the first day of preventive maintenance. This involves a complete internal and external mechanical inspection, including consumable component replacement. On the 2nd day the system will be on and off as we perform operational testing.
Day 1 includes mechanical inspection of:
- Combustion chamber
- Compressed air piping
- Gas train
- Dampers
- Poppet/Rotary valves
- Ceramic media
- Catalyst
- Insulation
- Fans
- Ductwork
- Exhaust stack
- Burner(s)
- Expansion joint(s)
- Control panels
- Plenums
- Flame safeguard unit
- Cold face
- External hot spots
Kono Kogs maintains a large inventory of replacement oxidizer parts. We also have our own fab shop and can produce custom components if necessary. Even more importantly, our team has the skills and knowledge to keep your process running reliably at peak efficiency.
Day 2:
The second day involves performance evaluation, including a complete review of system operation in on-line and off-line modes, electrical inspection and component testing. On day two the system will be started up and shut down to conduct process control and operational analysis.
Day 2 evaluation and testing includes but isn’t limited to:
- System startup cycle
- Online conditions
- Safety shutdown
- Alarms
- Valve cycling
- Pressure control loops
- Temperature profile
- Pressure/temperature controls
- Relays
- Test all safety switches/logic
- Burner tuning
- Burner controls
- Airflow switches
- Internal hot spot inspection/repair
- Thermocouples (replace TCs in combustion chamber)
- Actuators
- Motors
- Variable frequency drive (VFD)
- HMI & communication devices
- Data recorder
After each preventive maintenance visit you’ll get a detailed report including:
- Full checklist of system components & operations reviewed on site
- Work completed by technician
- Results of testing
- Critical findings requiring action
- Photo record of all areas, especially critical areas
- Recommended monthly maintenance plan
To better understand the level of inspection and detail covered during a preventive maintenance visit by Kono Kogs, view or download our RTO inspection sample report PDF:
KONOCare Gold
Everything in Silver
+ plus minimum remote support and reporting
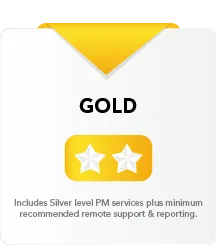
2 Customized for each system to meet your needs
KONOCare Platinum and KONOCare Gold include services that fall between Diamond (above) and Silver (below). Each KONOCare plan is optimized to suit your needs.
Share your application with us for a custom recommendation and quote.
All KONOCare plans include at least one annual onsite preventive maintenance visit.
Typically, preventive maintenance service takes place over two days. The air pollution control system will need to be shut down (and cooled) before our technician begins, and remain shut down for the first day of preventive maintenance. This involves a complete internal and external mechanical inspection, including consumable component replacement. On the 2nd day the system will be on and off as we perform operational testing.
Day 1 includes mechanical inspection of:
- Combustion chamber
- Compressed air piping
- Gas train
- Dampers
- Poppet/Rotary valves
- Ceramic media
- Catalyst
- Insulation
- Fans
- Ductwork
- Exhaust stack
- Burner(s)
- Expansion joint(s)
- Control panels
- Plenums
- Flame safeguard unit
- Cold face
- External hot spots
Kono Kogs maintains a large inventory of replacement oxidizer parts. We also have our own fab shop and can produce custom components if necessary. Even more importantly, our team has the skills and knowledge to keep your process running reliably at peak efficiency.
Day 2:
The second day involves performance evaluation, including a complete review of system operation in on-line and off-line modes, electrical inspection and component testing. On day two the system will be started up and shut down to conduct process control and operational analysis.
Day 2 evaluation and testing includes but isn’t limited to:
- System startup cycle
- Online conditions
- Safety shutdown
- Alarms
- Valve cycling
- Pressure control loops
- Temperature profile
- Pressure/temperature controls
- Relays
- Test all safety switches/logic
- Burner tuning
- Burner controls
- Airflow switches
- Internal hot spot inspection/repair
- Thermocouples (replace TCs in combustion chamber)
- Actuators
- Motors
- Variable frequency drive (VFD)
- HMI & communication devices
- Data recorder
After each preventive maintenance visit you’ll get a detailed report including:
- Full checklist of system components & operations reviewed on site
- Work completed by technician
- Results of testing
- Critical findings requiring action
- Photo record of all areas, especially critical areas
- Recommended monthly maintenance plan
To better understand the level of inspection and detail covered during a preventive maintenance visit by Kono Kogs, view or download our RTO inspection sample report PDF:
KONOCare Silver
Minimum recommended level of preventive maintenance
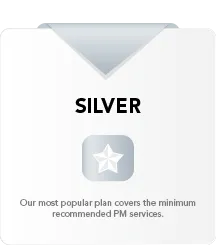
2 Customized for each system to meet your needs
All KONOCare plans include at least one annual onsite preventive maintenance visit.
Our KONOCare Silver package is our most popular package for RTO owners looking for baseline protection from unexpected downtime. KONOCare Silver includes an extensive annual RTO inspection. Details can be seen here.
All KONOCare plans include at least one annual onsite preventive maintenance visit.
Typically, preventive maintenance service takes place over two days. The air pollution control system will need to be shut down (and cooled) before our technician begins, and remain shut down for the first day of preventive maintenance. This involves a complete internal and external mechanical inspection, including consumable component replacement. On the 2nd day the system will be on and off as we perform operational testing.
Day 1 includes mechanical inspection of:
- Combustion chamber
- Compressed air piping
- Gas train
- Dampers
- Poppet/Rotary valves
- Ceramic media
- Catalyst
- Insulation
- Fans
- Ductwork
- Exhaust stack
- Burner(s)
- Expansion joint(s)
- Control panels
- Plenums
- Flame safeguard unit
- Cold face
- External hot spots
Kono Kogs maintains a large inventory of replacement oxidizer parts. We also have our own fab shop and can produce custom components if necessary. Even more importantly, our team has the skills and knowledge to keep your process running reliably at peak efficiency.
Day 2:
The second day involves performance evaluation, including a complete review of system operation in on-line and off-line modes, electrical inspection and component testing. On day two the system will be started up and shut down to conduct process control and operational analysis.
Day 2 evaluation and testing includes but isn’t limited to:
- System startup cycle
- Online conditions
- Safety shutdown
- Alarms
- Valve cycling
- Pressure control loops
- Temperature profile
- Pressure/temperature controls
- Relays
- Test all safety switches/logic
- Burner tuning
- Burner controls
- Airflow switches
- Internal hot spot inspection/repair
- Thermocouples (replace TCs in combustion chamber)
- Actuators
- Motors
- Variable frequency drive (VFD)
- HMI & communication devices
- Data recorder
After each preventive maintenance visit you’ll get a detailed report including:
- Full checklist of system components & operations reviewed on site
- Work completed by technician
- Results of testing
- Critical findings requiring action
- Photo record of all areas, especially critical areas
- Recommended monthly maintenance plan
To better understand the level of inspection and detail covered during a preventive maintenance visit by Kono Kogs, view or download our RTO inspection sample report PDF:
Customizing Your KONOCare Plan
In most cases we recommend an annual evaluation of all air pollution control equipment, though semi-annual or quarterly evaluations may be necessary depending on system complexity and the service requirements in your environmental operating permit.
RTO preventive maintenance visits can be flexible to accommodate your schedule. For example, a one-day preventive maintenance visit every six months instead of two consecutive days each year. Together we’ll design a program that meets your needs with minimal disruption to operations.
We can also bundle other oxidizer services with your preventive maintenance visit, including:
- New operator training (or refresher)
- Operating cost review
- Any pending aftermarket services
Remote Access & Troubleshooting
KKI also offers remote monitoring and troubleshooting services via our KONOConnect offering. These can be included as part of your customized KONOCare plan or billed hourly outside of our KONOCare program.
Benefits of Oxidizer Preventive Maintenance
Preventive maintenance offers several benefits directly affecting your bottom line:
- Minimize unplanned downtime & lost production
- Minimize oxidizer repair costs
- Extend the practical service life of your RTO
- Optimize equipment performance for energy efficiency
- Improve safety
- Establish a record of DRE compliance
Many states require facilities with thermal oxidizers to keep records of their equipment maintenance program. Fines can be issued for noncompliance in record-keeping, even if the system is operating properly. If a device fails to meet the control requirements defined in the permit, the monetary penalty can be significant, and also gets you “noticed” in a way that you don’t want – another good reason to create and maintain a regular DRE compliance record.
The experts at Kono Kogs give you peace of mind, keeping your oxidizer operating and compliant, energy costs in check, and interactions with the EPA to a minimum.
Request Service Form
Please fill the form below to receive a service quote. You can also call us 24/7/365 at 920-461-9078 or send us an email.