Custom Built Regenerative Thermal Oxidizer (RTO) Treating Food Packaging Emissions
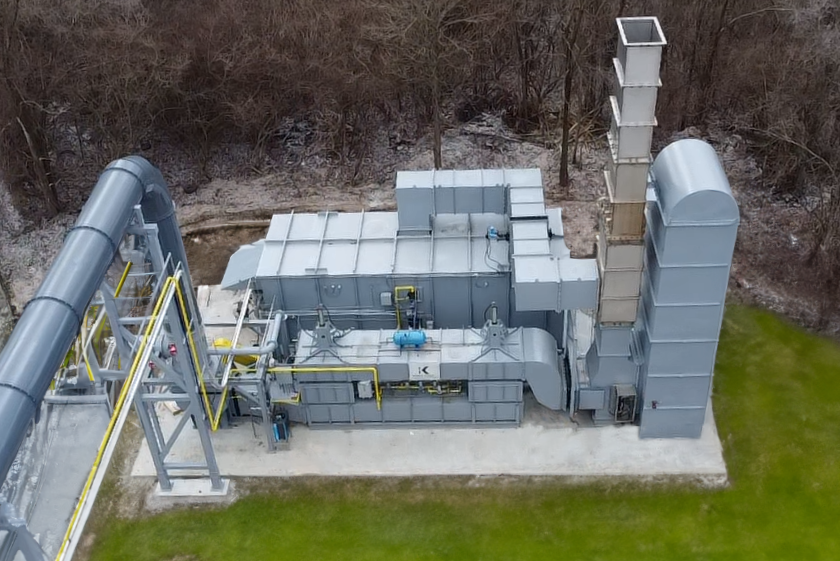
Kono Kogs designed, fabricated & installed a custom RTO at a food packaging manufacturer
Problem
A leading supplier food packaging was expanding, include the addition of a new flexographic printing press. Emission control for the press exhaust was required, along with additional capacity for existing presses which were being treated by an older catalytic oxidizer. A regenerative thermal oxidizer (RTO) was the preferred oxidizer technology. The new RTO would replace the existing system and providing increased VOC destruction efficiency and significant utility savings. In addition to the RTO, process ductwork and dampers were needed, as well as mechanical installation on the customer's concrete pad.
Additional project requirements were for very high VOC destruction efficiency, as well as the ability to handle high VOC concentrations emitted by today's highly recirculating printing presses.
Solution
Kono Kogs typically has over 25 existing RTO systems in our inventory, of only the best-built OEM/models, in multiple capacities and types. But for this particular application we did not have a match desired by the customer: 25,000 scfm capacity with poppet style switching valves, hot gas bypass system, and a puff capture feature. A custom RTO was proposed which included a VOC entrapment (puff capture) option, and a hot gas bypass feature.
Our custom RTO systems have the best of the best, industry-proven technology, all designed to meet our primary aim of extreme reliability and long life. The RTO meets that aim with an intuitive and innovative (yet simple) design. Our custom RTO design was a cumulative effort of our exceptional engineers and designers holding decades of experience designing oxidizer systems for nearly every industrial application.
This was our 4th project together with this food packaging manufacturer, and our second system installation for them. The first unit was a successful, refurbished 16,000 scfm RTO in 2023. We value partnerships like this one; we seek to optimize our customer's capital spending with common sense, ultra-reliable oxidizer solutions and provide exceptional after-sale support, from remote monitoring, to preventive maintenance schedules and reminders, and well stocked spare parts inventories. All in an effort to be a reliable partner in the successful emission control of their printing emissions.
Equipment & Services Provided
- Custom Built RTO w/structured media & poppet valves
- Ship & mechanically assemble RTO
- Fabricate all process ductwork & T-dampers
- Equipment and crew to install RTO and ductwork
- Equipment commissioning
- Parts & VOC destruction warranty
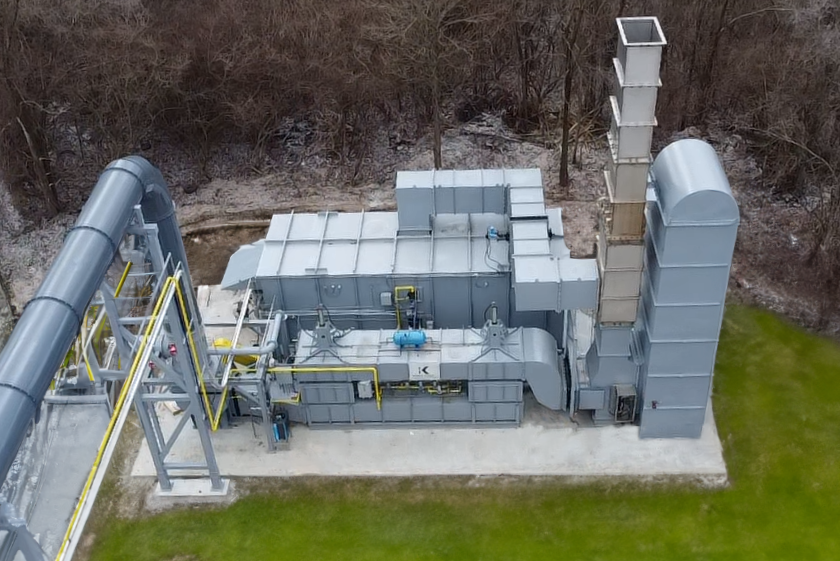
Results
The partnership between Kono Kogs and our customer resulted in an exceptionally well-performing new (& refurbished/hybrid) RTO. The project completed on time and on budget, with extremely low process down-time needed to make the switch over from the catalytic oxidizer to the new RTO system.
Our customer/partner has recently purchased a new, larger, custom RTO system from Kono Kogs. The purchased hinged on one important condition. The main requirement was that the same Kono Kogs personnel be assigned to the project who worked on the 25,000 RTO project. High praise that we appreciate hearing. We also know that it brings high expectations, which we certainly intend to live up to. Of course, we assigned the same team (though we believe all of our teams are exceptional).
What is different about Kono Kogs?:
New & Refurbished Come Together: While the main RTO body consisting of the ceramic media chambers, combustion chamber and poppet valves was designed and built from the ground up in our shop for this project, the peripheral pieces were sourced from our large inventory of existing components, resulting in exceptional cost savings for our customer. The peripheral components consisted of an existing fan, and existing VOC entrapment (puff capture) system, burner, and isolation dampers.
Vertical Integration: We are vertically integrated, meaning we are able to design, fabricate, assemble, ship, install and commission your oxidizer system with our people, and install it anywhere in the USA. No third parties. Just our talented fabrication team forming and assembling the innovatively simple RTO design, controlling quality and timelines. Our in-house fabrication capability also benefits our customer's bottom line as there are no "middle-man" mark-ups for fabrication work. And throughout the project it is our team communicating seamlessly with our partner's team to accomplish a successful project, on time and on budget. Our on-site crews are our crews, led by our crew leaders, at the direction of our project engineer, working in partnership with your team. All with the high level safety training and insurance coverage you should expect from your suppliers.