RTO w/Installation & Ductwork Treating Metal Decorating Emissions
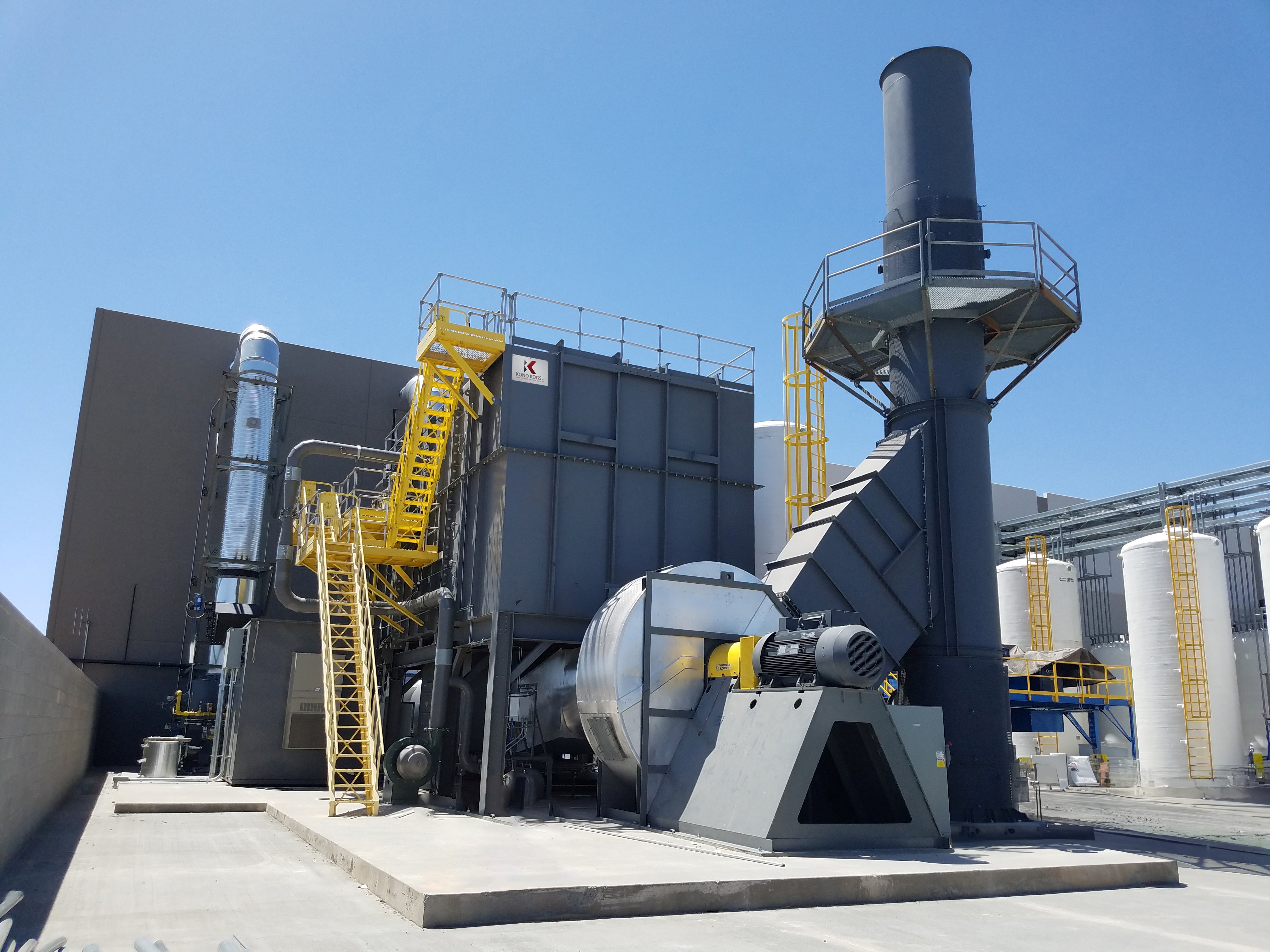
New metal can coating facility had several ambient airstreams & several hot airstreams to treat. Our RTO met or exceeded all customer demands for this project.
Problem
A metal decorator (can coater) was expanding. The new facility had several ambient airstreams and several hot airstreams to treat. If mixed, the hot emissions from the inside bake oven (IBO) and pin oven containing high boiling point solvents would condense out when mixed with the cooler emissions drawn from the inside spray area. Condensate inside ductwork and RTO components leads to low reliability, extensive cleaning, fan balancing problems, and presents a fire hazard. Reliability and knowledge of the customer’s process were to be the critical factors in the choice of a supplier for this project.
Photos: In Progess
Click on a picture to enlarge
Solution
Kono Kogs had a wide variety of RTO sizes and technologies available in our industrial oxidizer inventory. The MEGTEC Clean Switch RTO was the best match as a base system. The Durr-MEGTEC Systems Clean Switch RTO is a proven performer for a wide variety of emission airstreams. The low pressure drop of the system, the robust design, combined with an innovative rotary switching valve make it the system of choice for rotary valve RTOs.
A rotary switching valve was a specific customer requirement for this project. Poorly tuned or poorly designed poppet valve can tip cans over in the ovens causing unacceptable production line shutdowns. Rotary valves produce little-to-no pressure pulses.
To accommodate the mixing of cold and hot air sources, a mixing box was added prior to the RTO and the fan was relocated to the exhaust end of the RTO (induced draft design). A PLC upgrade to an Allen Bradley Controllogix platform was also included, along with remote monitoring capability.
Kono Kogs provided the shipping of the RTO to site, rigging and mechanical assembly on the customer’s pad. We also provided all power and control wiring, as well as, gas and compressed air piping and commissioned the RTO and supplied an extensive spare parts package.
Photos: After
Click on a picture to enlarge
Equipment & Services Provided
- Fully Refurbished Used Regenerative Thermal Oxidizer (RTO) Performance and Parts Warranty Rigging/Mechanical Assemblyli>
- Power & Control Wiring
- Gas & Air Piping
- Equipment Commissioning
- Mixing Box
- Induced Draft Fan (reconfigure)
- New Exhaust stack
- PLC Upgrade (Controllogix)
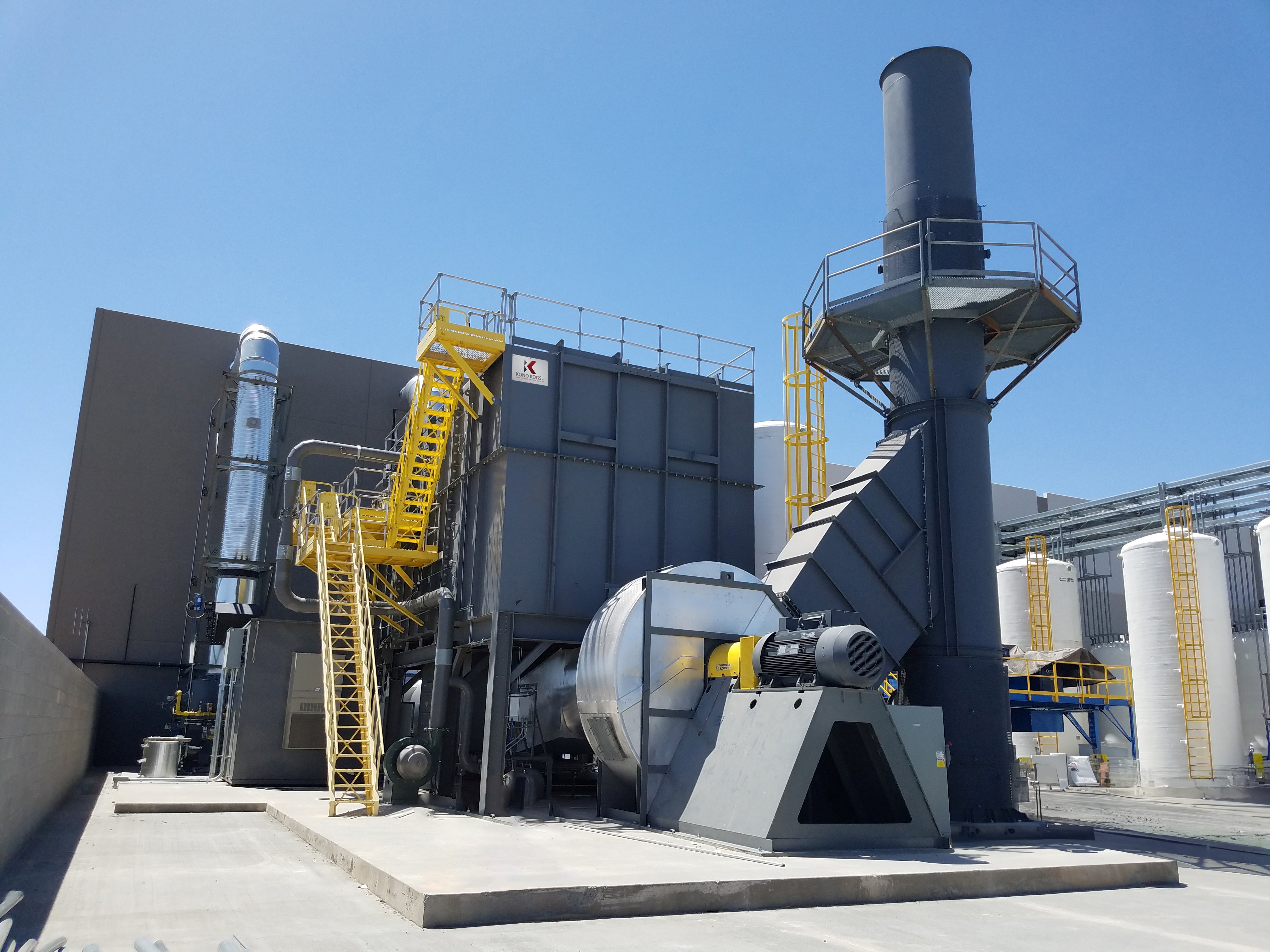
Results
RTO met or exceeded all customer demands for this can coating project. This was the second of several successful RTO systems provided to this customer with the same configuration. We are grateful for the continued confidence from one of our many repeat customers.