Regenerative Thermal Oxidizers: What they are, what they do, and more
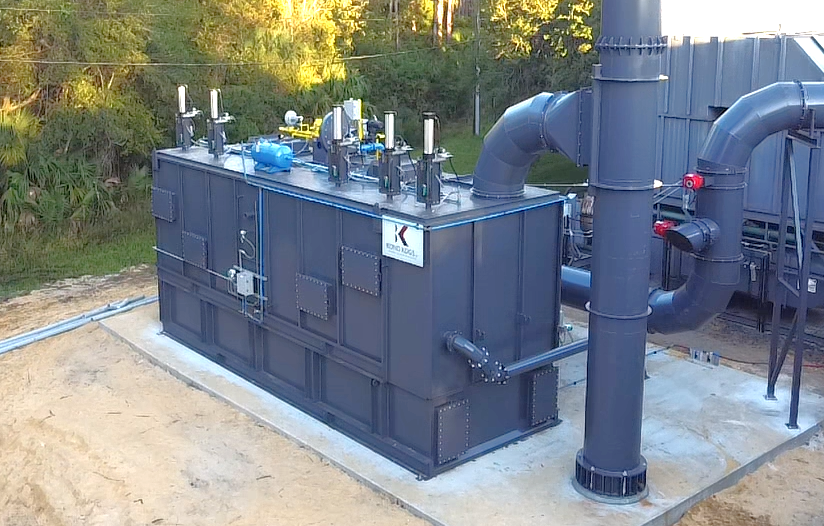
RTO systems destroy VOCs in industrial exhaust air to reduce air pollution.
A regenerative thermal oxidizer (RTO) is a type of air pollution control equipment that destroys hazardous air pollutants (HAP), volatile organic compounds (VOC) and odorous emissions created during industrial processes. A key difference between an RTO pollution abatement system and other oxidizer types is regenerative heat recovery, which makes the system extremely fuel efficient. For many reasons RTOs are the most common oxidizer technology in use today.
RTO Basics
RTO Operating Principles—RTO technology collects air emissions from industrial exhaust airstreams containing VOCs and HAPs, raises the airstream to high temperature to oxidize (convert) the pollutants into CO2 and H2O before releasing the clean airstream into the atmosphere. Like other oxidizer systems, time, temperature, and turbulence are the key to proper performance of an RTO.
Common Initial Questions
The term “regenerative” in regenerative thermal oxidizer is drawn from the type of ceramic media heat exchanger used in these systems. It is unique in that it captures heat from the exhausting, clean airstream during one cycle and releases the heat to the incoming, dirty airstream in the next cycle. The heat is captured (and released) from beds of ceramic media. The RTO incorporates switching valves to cycle the direction of the airflow through the RTO heat exchanger beds to enable regenerative heat recovery.
Regenerative thermal oxidizers have a heat recovery (efficiency) of 95% typically. This technology has the lowest operating cost of all thermal oxidizer systems – not to mention the longest service life and highest reliability. It’s even possible for an RTO to operate with no auxiliary fuel use whatsoever if process VOC concentration levels are >3-4% lower flammability limit (LFL).
Clean process airstreams with high air flow and low VOC content (<10% LFL) are ideal applications. Higher VOC concentrations can be tolerated, as well as organic/inorganic particulates with proper planning and design, and possibly filters. See our case studies for a sample of possible applications.
RTOs typically operate at 1500o – 1600o Fahrenheit depending upon the VOC characteristics. Thermocouples inside the chamber monitor temperature and adjust gas burner firing as needed. Adequate temperature is essential to ensure VOC destruction efficiency. In most cases a data log of chamber temperature is required for air quality compliance.
RTOs typically have a 0.5 second to 1.0 second dwell time for most applications.
The Regenerative Thermal Oxidizer Process
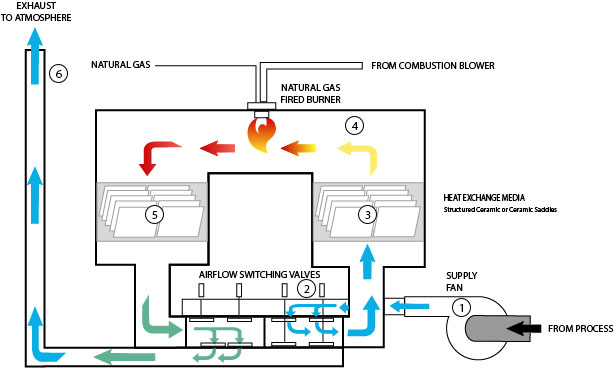
The Simple RTO Process
An RTO uses six basic steps for each cycle to heat the incoming dirty air, burn off pollutants and cool the exhausted clean air.
- Polluted air is drawn into the RTO fan
- Polluted air is pushed through a valve system into one (of two) beds of ceramic media
- Air is pushed through heated ceramic media; heating the air while cooling the ceramic media
- Heated air is pushed into a combustion chamber where pollutants are burned off
- Clean, hot air is pushed into second (of two) beds of ceramic media; giving off heat to the ceramic media, cooling the air
- Clean, cooled air is pushed through open valve and exhausted into the atmosphere
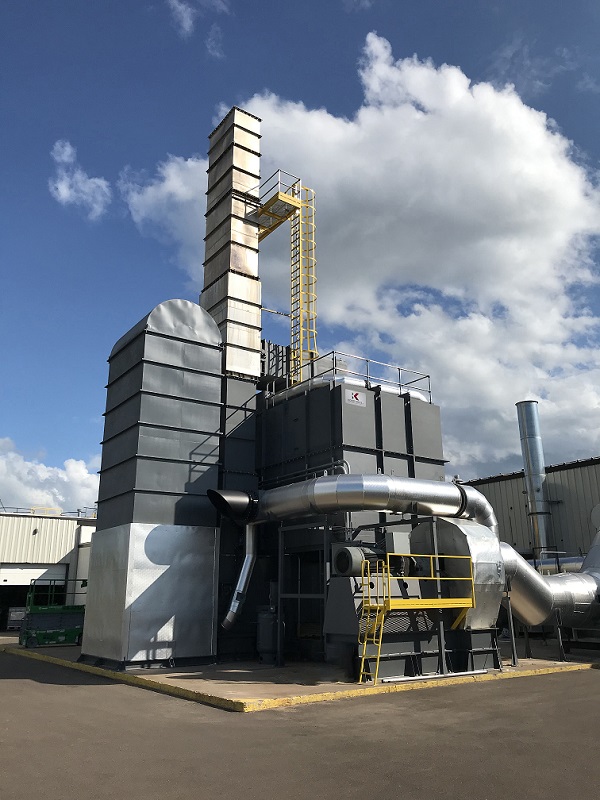
Types of Regenerative Thermal Oxidizers
While RTOs can come in a few different configurations and layouts depending on the system’s requirements, the number of heat chambers used is the most common differentiator between types of RTOs. Also, there are variations in the types of valves used to reverse airflow direction. Some RTO technologies may not incorporate a traditional combustion chamber at all.
Essential differentiators between types of RTOs are:
- Chamber Configurations
- Heating Techniques
- Air Flow Valves
LEARN MORE - Types of Regenerative Thermal Oxidizers
Applications of Regenerative Thermal Oxidizers
RTOs are used by manufacturers in a wide range of industries and applications. The Kono Kogs team has experience with practically every possible oxidizer application across many industries around the globe.
Industry Processes Using RTOs to Treat Emissions
- Printing
- Industrial Painting
- Electronics Fabrication
- Material Coating
- Chemical Processing
- Lamination
- Can Production
LEARN MORE – RTO Industry Applications
How much does a regenerative thermal oxidizer (RTO) cost?
RTOs are sized and priced based on airflow volume that the system will treat. Total Cost of Ownership (TCO) is the initial capital investment in the equipment, plus installation costs, plus operating costs (fuel, electricity, and compressed air).
- RTOs have the lowest operating cost compared to other types of thermal oxidizers.
- Lower cost units often have higher operating costs and lower reliability due to inferior components, and a design operating on its outer limits.
- Fully refurbished RTO systems from Kono Kogs can save you 40% or more in capital costs compared to buying new – with comparable guarantees and warranties
OR
Contact the KKI team for help selecting the most cost-effective RTO system for your application. We can turn quotes around within 24 hours for common applications. When special features are required, like hot gas bypass, puff capture, special metals, etc. a little more time will be needed to complete the quote.
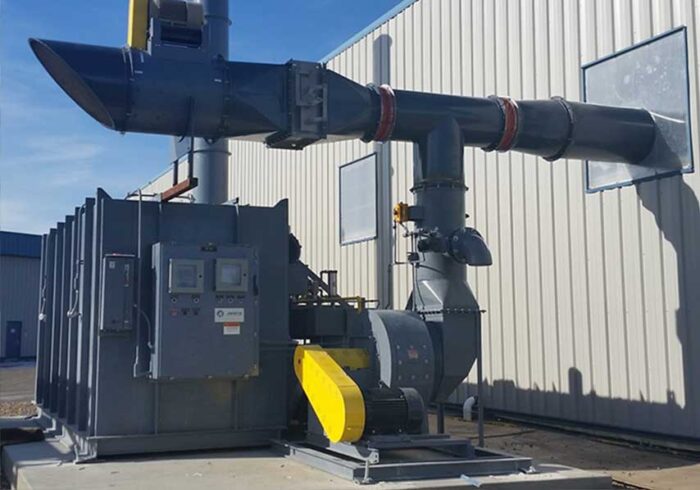
Regenerative Thermal Oxidizer Design Factors
Certain RTO design factors can make a significant difference in both capital and operating costs:
- Process air volume flowrate affects the size of the RTO unit, dampers and ductwork you’ll need.
- Process air exhaust temperature determines the need for ductwork insulation, fan sizing, and affects expected operating costs.
- Type & concentration of pollutants affects material of construction, heat exchanger efficiency, and greatly determines operating costs of electricity and fuel.
- Complexity of RTO design affects how much RTO maintenance will be required. RTOs come in different designs, sizes and configurations.
- Projected growth could make it smarter to install a higher-capacity system right away, rather than adding a second RTO in the future.
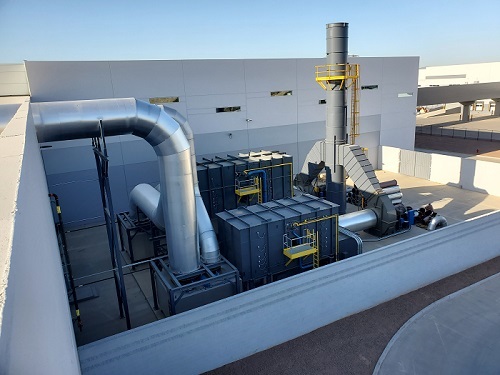
RTOs Compared to Other Pollution Abatement Systems
Regenerative thermal oxidizers have many advantages over other oxidizer designs, but application in a specific process must be evaluated to determine whether it is a good match for your emission control needs.
Regenerative Thermal Oxidizer vs Thermal Oxidizer
In thermal oxidizers, air flows only one direction through the system. RTOs however create airflow reversals using dampers and control logic, which makes them much more thermally efficient.
Compared to other thermal oxidizer systems, regenerative thermal oxidizers are more efficient and reliable, and have a longer service life. However RTOs have a more complex build and are heavier, which can affect shipping, installation and commissioning costs.
RTOs are the best option for most industrial processes, however when 99.99% destruction of VOCs is a requirement, a thermal recuperative oxidizer may be the better solution.
LEARN MORE – Regenerative Thermal Oxidizers vs. Thermal Oxidizers
Regenerative Thermal Oxidizer vs Recuperative Thermal Oxidizer
The main difference between regenerative and recuperative thermal oxidizers is how each one recovers heat while operating. Recuperative thermal oxidizers use metal as the heat exchange material, while regenerative thermal oxidizers use ceramic media.
Regenerative Thermal Oxidizer Components
In many cases, KKI can help businesses comply with environmental regulations and reduce operating costs by repairing, rebuilding, or upgrading their existing regenerative thermal oxidizer. We have an extensive inventory of RTO parts including ceramic media, fans, burners, and much more, plus an in-house fabrication shop.
When the cost of regenerative thermal oxidizer repair outweighs the benefit, KKI can facilitate RTO replacement. We offer fully refurbished systems with parts and performance warranties.
Available RTO components from Kono Kogs
- Exhaust stacks
- Combustion chambers
- Media chambers
- Media cold face support
- Gas trains
- Process ductwork/supports
- Process T dampers
- Hot bypass valves
- Access platforms
- PLC cabinets
- Actuators
- Insulation & cladding
- Pneumatic controls
Kono Kogs RTO upgrades/services
- Ceramic media change outs & upgrades
- Fan balancing/rebuilds/relocation
- Damper replacement
- PLC programming & upgrades
- Burner/gas train upgrades
- Turnkey capture systems
- Exhaust stack reconfiguration
- Fan motor rebuilds
- Preventive RTO maintenance programs
- Remote monitoring hardware/software
- Full turnkey installation
The components and services above are by no means comprehensive. KKI can handle any RTO rebuild or replacement project you are facing. We invite you to send us your trickiest projects; we look forward to the challenge!
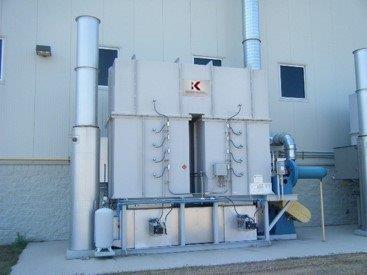
Regenerative Thermal Oxidizer Manufacturers
The best-built RTOs make the best used RTOs. KKI selects only the best pre-owned regenerative thermal oxidizers and stands behind them with warranties that match new equipment Original Equipment Manufacturer (OEM) warranties. Check out our current RTO inventory from manufacturers including:
- CECO ADWEST Technologies
- Dürr MEGTEC Systems
- CMM Group
- REECO (Dürr)
- TANN Corp.
- Alstom
Common Questions When Researching RTO Systems for Pollution Abatement
RTO systems are advanced pollution control systems, so doing the required research before selecting the best one for your needs is essential. Below are some important questions our clients often consider before moving forward with purchasing a new or used system. Of course the engineering team at Kono Kogs is always available to answer questions and advise clients on the best RTO options for their needs.
For examples of our work, check out these refurbished and new RTO case studies by Kono Kogs.
- Maximum thermal efficiency
- Lowest pressure drop
- Ability to handle organic/inorganic particulates
Fuel injection can provide significant fuel savings
Special materials of construction may be required
A puff capture feature can help eliminate visible emissions
VFDs are important for efficient operation, volume turn-down and idle operation
Solvents with a high boiling point can build up on a forced draft fan wheel
Rotary valve technology may be a better option
Ease of installation results in lower turnkey cost
Remote access can ease troubleshooting and reduce the frequency of service visits
A bake-out feature can address organic compound build-up
Please check our RTO Inventory...Quality-built refurbished regenerative thermal oxidizer (RTO) systems have a long life, can save 40% vs. new units, and have performance and parts warranties comparable to new systems.
Regenerative Thermal Oxidizer Treating Coil Coating Emissions
Case Study: the used RTO from KKI had excellent performance numbers (99% VOC DRE) and provided significant capital cost savings compared to new equipment.
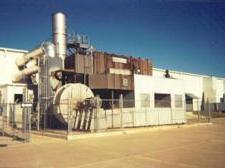
KKI is the leading global supplier of high-quality used air pollution control equipment. Our team has a 100% success rate meeting our performance guarantees and has earned repeat business from multiple customers. Whether you’re looking to get more efficient service out of your existing RTO or learn about your replacement options, KKI can help.