How much does a regenerative thermal oxidizer cost?
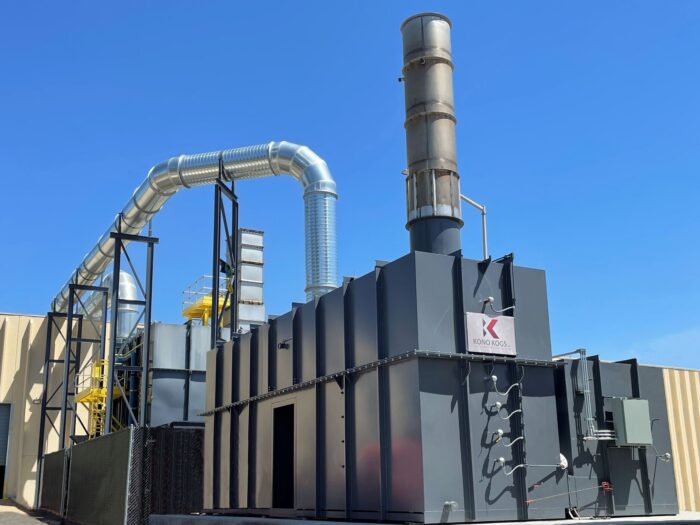
RTO Cost Factors
The cost range for a new RTO system depends on the size, features and quality of the system. Airflow capacity is the primary driving cost factor, followed by necessary features, then the quality of materials of construction and components.
Total Cost of Owning a Regenerative Thermal Oxidizer
Regenerative thermal oxidizer systems are designed to treat a specific amount of polluted air, and the system cost is driven by the amount of air that the RTO is designed to treat. As a general rule, cost efficiency increases with the size of the system; larger units achieve economies of scale.
There are other very important factors to consider along with the initial capital cost of the RTO, including:
- Operating cost
- Installation costs
- Shipping
- Concrete pad
- Ductwork & Dampers
- Equipment commissioning
- Maintenance cost
After equipment cost, the next greatest cost factor will be operating costs; this includes fuel and electrical costs to run the RTO for its multi-decade lifespan. Be aware that low-cost RTO systems may have significantly higher operating costs than a higher-cost RTO system. Lost production costs from unreliable RTO can easily exceed the cost of the entire RTO system. Choose wisely.
For more discussion on evaluating your RTO proposals, check out purchasing new or used thermal oxidizing system and our article in Process Heating magazine.
Design Factors Affecting RTO Cost
Certain RTO design factors can make a significant difference in both capital and operating costs:
- Process air volume flowrate affects the size of the RTO unit, dampers and ductwork you’ll need.
- Process air exhaust temperature determines the need for ductwork insulation, fan sizing, and affects expected operating costs.
- Type & concentration of pollutants affects materials of construction, optimal heat exchanger efficiency, and greatly determines operating costs of electricity and fuel.
- Complexity of RTO design affects how much RTO maintenance will be required. RTOs come in different designs, sizes and configurations.
- Projected growth could make it smarter to install a higher-capacity system right away, rather than adding a second RTO in the future.
RTO Flow Resistance and Electric Costs Comparisons
Fan Power
Since some RTOs have higher flow resistance (pressure drop across the oxidizer) than catalytic and recuperative thermal oxidizers, the fan power required to move air through the oxidizer can be higher than what’s required for those systems, resulting in comparatively higher electric costs.
Structured Media
Most modern RTO designs achieve lower electric operating costs by using structured media to heat the polluted air. While structured media should not be used for some particulate-laden streams, the energy savings possible in most RTO applications easily offset the cost for an upgrade to structured ceramic media vs. random ceramic media. Additionally, structured ceramic media has become more common as prices drop.
Verdict
So, for high airflows and light VOC concentrations, the regenerative thermal oxidizer still provides significantly lower overall operating costs than catalytic or recuperative thermal oxidizer systems because of the RTOs fuel efficiency. In fact, a recuperative thermal oxidizer will likely always be more expensive to operate than a regenerative thermal oxidizer.
Other Considerations: Design Limitations & Puff Capture Retrofit Options
Most regenerative systems use a two-chamber design, typically achieving over 98% VOC destruction efficiency. An RTO’s fuel efficiency is achieved by utilizing a repeating flow-reversal. This reversal of flow (occurring about every 3 minutes) causes a puff of dirty air to exit the exhaust stack. When the flow control valves switch position, a small portion of the contaminated air becomes trapped momentarily, then is back-flushed out to the exhaust stack.
When visible emissions are present, such as heavy condensables or long-chain hydrocarbons, the back-flushed air will be visible as it exits the oxidizer exhaust stack. In general, if the process exhausting to the RTO has a visible exhaust, it will have a visible puff during every valve switch. While the oxidizer still maintains an overall 98+% VOC destruction efficiency, the puff can be a nuisance issue if a facility is near a residential area. Options sometimes called puff capture or VOC entrapment are available to capture this puff of emissions. Kono Kogs can retrofit RTOs with this option; and many new RTOs are being configured with this feature as well.
Trends Affecting Regenerative Thermal Oxidizer Cost
RTOs are by far the technology of choice for most applications today because they offer high VOC destruction efficiency, reliability, and most importantly, fuel efficiency. There have also been a few advancements which further separate RTOs as the type of thermal oxidizer with the best overall value. From new design efficiencies to scaled-back flow VOC concentrations, these new developments will have an impact on cost and the range of applications they can service.
Valve System Efficiency
Poppet Valves
Poppet valve designs have been proven over the 25+ years they have been used for RTO systems. Some designs over-complicate poppet valve operation and should be avoided, or added maintenance downtime should be planned into your production schedule.
Rotary Valves
Another switching valve technology is a rotary valve RTO. These have been around for over 15 years and a few of them have proven reliable. They can be maintenance challenges in certain applications. Also, certain systems are more maintenance-intensive due to the ceramic bed separation design. Others have the bearing for valve rotation exposed to high temperatures, leading to frequent maintenance or failure.
Rotary valve technology has evolved to where these valves are proven and reliable performers. Installing or retrofitting electric drives (motor, VSD) in cold weather locations has addressed a common issue of freeze ups experienced in pneumatic lines of these rotary valves.
Lower Flow Efficiency in RTOs
Originally designed for high airflow rates with low VOC concentrations, recent advances in regenerative thermal oxidizer designs has allowed economical control of small emission airstreams (<3000 scfm) as well. Advancements in structured ceramic media have allowed RTO systems to operate at horsepower rivaling catalytic systems and sometimes lower. And structured ceramic media prices now allow fast payback over random packed media systems.
Material Costs
The steel, ceramic and other materials used to build a regenerative thermal oxidizer can vary in price dependent on various market factors. In cases where it's recommended there can be many advantages to buying a refurbished RTO rather than a new one in order to bypass these material costs.
Consult with Industrial Air Pollution Abatement Specialists
The Kono Kogs team has over 150 years of combined experience designing, reconditioning, and installing all types of thermal oxidizer systems, especially RTOs. We’re happy to perform a cost-benefit analysis for your project, explain your options, including the trade-offs of each, and provide a professional recommendation.
A regenerative thermal oxidizer is a significant investment, but it doesn’t have to be a major long-term expense. Contact the KKI team for help selecting the most cost-effective system for your application.
Fully refurbished RTO systems from Kono Kogs can save you 40% or more in capital costs compared to buying new – with comparable guarantees and warranties.
Additional Cost-related RTO FAQs
Get quick answers to some common questions related to regenerative thermal oxidizer costs. Feel free to contact us with any further questions.
Regenerative thermal oxidizers have a heat recovery (efficiency) of 95% typically. This technology has the lowest operating cost of all thermal oxidizer systems – not to mention the longest service life and highest reliability. It’s even possible for an RTO to operate with no auxiliary fuel use whatsoever if process VOC concentration levels are >3-4% lower flammability limit (LFL).
This is a common concern. Will the buyer be left with only promises, or will Kono Kogs provide robust support after the purchase and commissioning of the oxidizer? We have never failed to meet our warranty in either parts or oxidizer performance. We have references that will attest to this in every business size- from start-up companies, to growing small, and mid-size companies, to Fortune 500 companies. Our experienced staff can handle any technical or maintenance issue, both on-site, and via remote monitoring to ensure a successful project, now and into the future with our long-life refurbished oxidizers.
Our warranty rivals that of new equipment OEMs and we can even extend the period, if desired. How do we do that? We offer only the best built systems from the best names in the industry. We also perform extensive sub-system and parts checkouts and replace faulty or questionable parts, many times with upgraded parts. Our goal is a flawless project- achieved with proper planning and with our staff’s extensive oxidizer experience. We are honored that our customers are our best advocates. They affirm that we deliver what we promise- which has been true since day one of Kono Kogs.
Please check our RTO Inventory...Quality-built refurbished regenerative thermal oxidizer (RTO) systems have a long life, can save 40% vs. new units, and have performance and parts warranties comparable to new systems.