Regenerative Thermal Oxidizer Treating Encapsulating Line Emissions
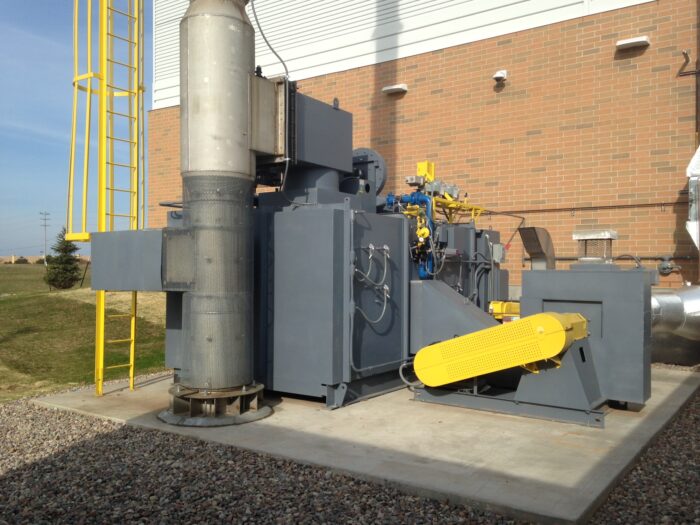
Our refurbished RTO system for an encapsulating company provided low TCO (capital cost, operating cost, maintenance cost) & significant savings over new.
Problem
After proving out a spray dryer in their R&D lab over many years, an encapsulating company set out to offer commercial encapsulating on a larger scale. Although the emissions were light in concentration, the potential odor from the wide variety of materials to be encapsulated was the main concern. Also, there was a potential for dust/particulate material that had to be addressed. The RTO would need to provide a bypass feature (fan/dampers) because the RTO fan will be the only source of exhaust air from the new building.
Photos: In Progess
Click on a picture to enlarge
Solution
We had several small RTO systems in our inventory that could have performed well for this application. Based on a total cost of ownership (TCO) analysis (Selecting an Oxidizer) we recommended a MEGTEC Millennium 4000 regenerative thermal oxidizer. This system provided the lowest TCO (capital cost, operating cost, maintenance cost) of the RTO’s that we had available, and significant cost savings over a new RTO system.
We received the contract for the RTO and an inlet filter, as well as a plant exhaust fan and diverting damper. We also provided mechanical assembly, gas piping, compressed air piping, and electrical wiring. Our customer provided the required stainless steel ductwork (stainless steel needed due to the potential for halogens in the airstream) and the concrete pad.
We recommended quarterly preventive RTO maintenance inspections initially to determine the impact of particulate build-up. Pressure profiles were taken at the start-up of the RTO for monitoring purposes. This is a single process RTO with fixed airflow, so as particulate builds up (if it does) we will be able to track increases in pressure drop across the RTO to identify the plugging as it occurs.
Photos: After
Click on a picture to enlarge
Equipment & Services Provided
- Fully Refurbished used Regenerative Thermal Oxidizer (RTO)
- Performance and parts warranty
- Refurbished and repainted regenerative thermal oxidizer
- Low Capital Cost: Approximately 60% of the cost of a new system
- Energy efficient: 94% heat exchanger effectiveness with structured media
- Back-up/bypass fan with diverter damper for facility exhaust
- RTO is the exhaust fan for the entire facility
- Older model (12 year old) RTO system with another 20+ year life expectancy
- PLC program updates to accommodate customers process and the new bypass fan
- Mechanical assembly, electrical wiring, gas/air piping, ductwork guidance, permit assistance, trucking to site, and process air handling guidance
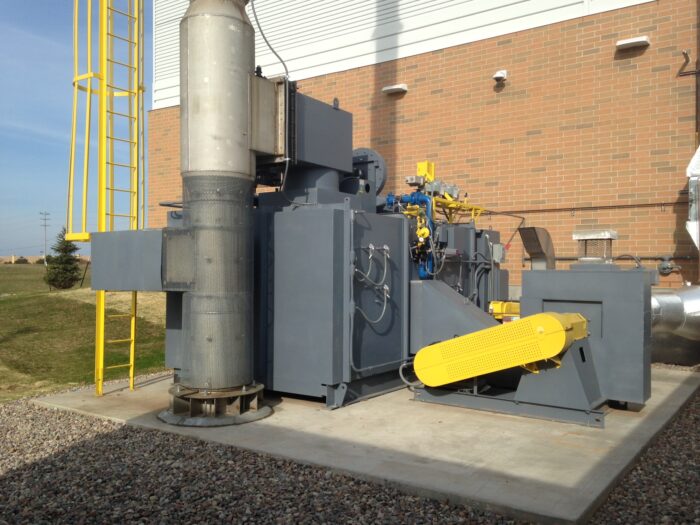
Results
RTO met or exceeded all customer demands for this project at 60% of the cost for a new system. This system was well built just needing most of its mechanical parts replaced due to non-use. The result was a low cost, reliable, refurbished regenerative thermal oxidizer.
Used regenerative thermal oxidizers have a long life due to the simplicity of the design. The shell of the unit is critical, as well as, the insulation that protects it, so it is important that these components along with the poppet (or rotary) valves are sound. A high-quality RTO system is also critical. Inferior components make an inferior RTO. We know the Millennium RTO is a well-built system, and know its potential problems (original ceramic media needs to be replaced due to media shifting), so we can confidently refurbish this model and guarantee the performance and parts for significant periods; and offer extended warranties that match new equipment, if desired by our customers.