What is a VOC Puff Chamber?
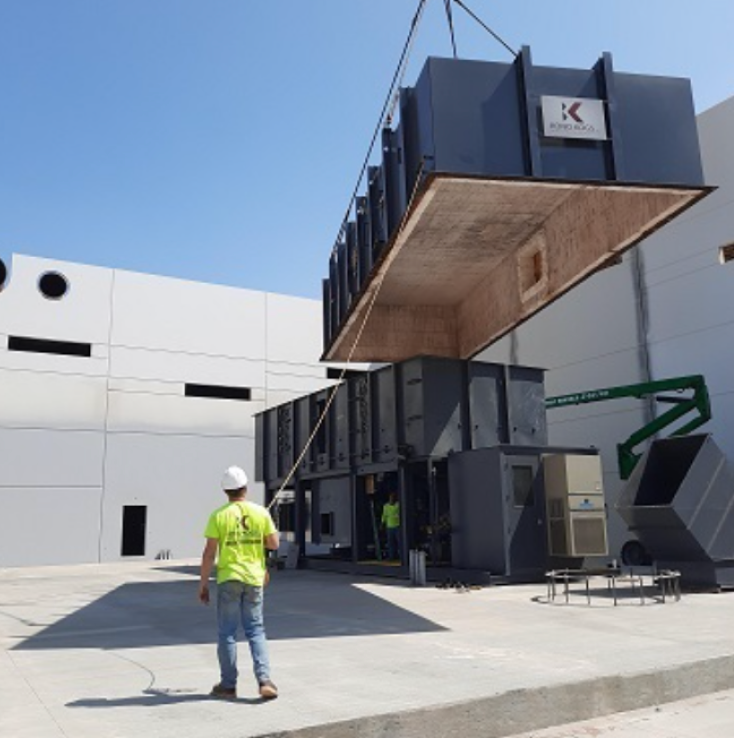
Enhance the operation of your RTO with a VOC Puff Chamber
A VOC puff chamber (a.k.a. VOC entrapment chamber) is a specialized component in regenerative thermal oxidizers designed to capture and eliminate slugs of non-treated process air, known as "puffs," that occur during valve switching. These puffs can limit the destruction rate efficiency (DRE) of the unit and cause unpleasant odors or visible emissions. The puff chamber redirects this captured, dirty air back to the RTO's inlet for further treatment, ensuring higher efficiency and cleaner emissions.
What does a Puff Chamber do?
One issue with two-can regenerative thermal oxidizers is the presence of a slug of non-treated process air (known as the “puff”) that exists during valve switching. It occurs when a chamber on “inlet mode” is switched to “outlet mode,” and the process air that just entered the cold face plenum and the lower section of the heat recovery media reverses directions and is sent up the stack. Such puffs both limit the maximum DRE of the unit and can also cause an unpleasant odor or visible emission depending on the constituents of the air stream being treated. For greater context see: How Does an RTO Work?
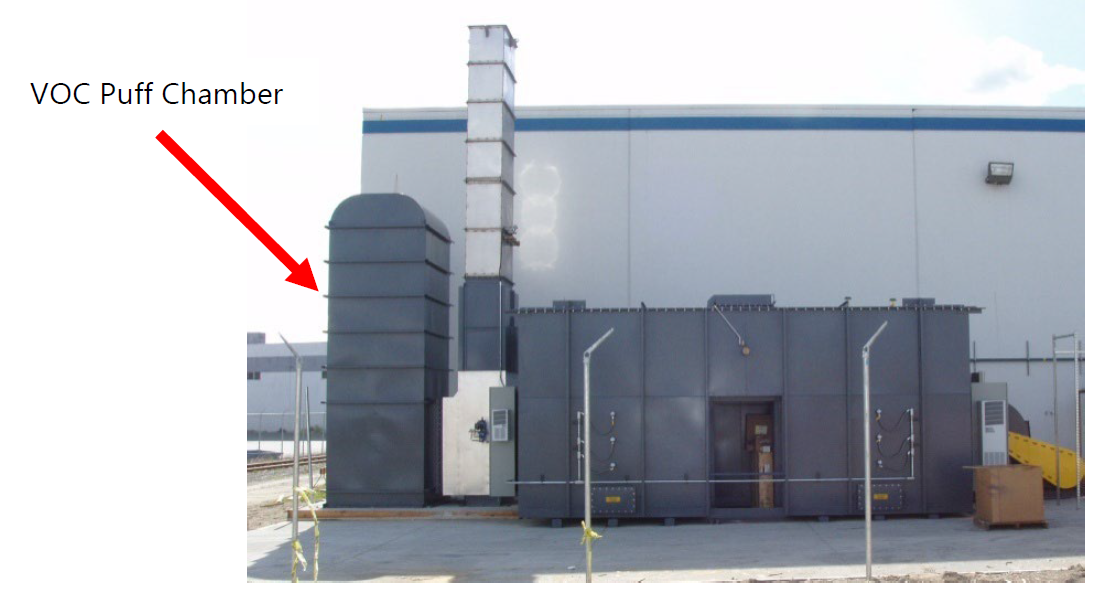
Impact on Destruction Rate Efficiency (DRE)
Without a puff capture feature, this puff of dirty air will be sensed on the field destruction test chart. If the inlet VOC concentration becomes low, the puff will have an outsized impact on the testing results. The differential VOC concentration from the RTO inlet to the outlet will become less, which may lead to a failed stack test.
Puff Chamber Solution
This unit is equipped with a ‘puff chamber,’ (a.k.a VOC entrapment chamber) which is a third chamber where the dirty air is directed during a valve transition. This captured air is then directed back to the inlet of the RTO to further destroy the VOCs/odors and eliminate the puff or subsequent odor.
The formula used to calculate destruction rate efficiency (DRE) is as follows:
Destruction Rate Efficiency = (Inlet Concentration−Outlet Concentration/Inlet Concentration) × 100
Most OEMs use a ‘puff chamber’. This is the least expensive puff capture option as it does not contain ceramic media and does not need to be internally insulated.
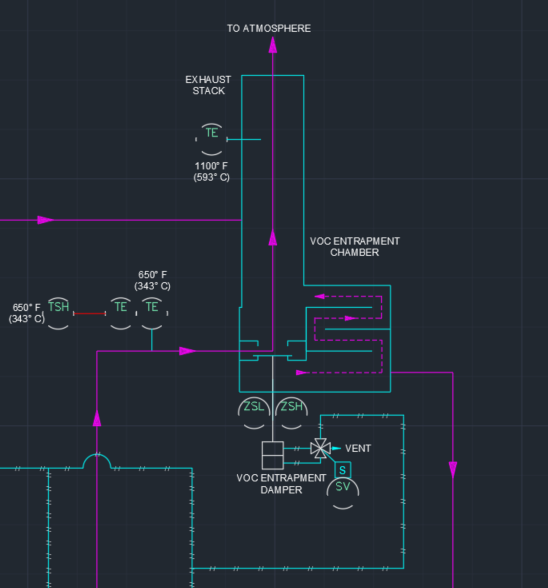
Other "Puff" Solutions
Another way to control the puff is by employing a cascading purge sequence with an odd number of media beds. During the heating/cooling cycle, each bed passes through inlet/purge/outlet modes in that order. After a bed is used as inlet, it is purged, and any dirty air remaining in the bed is evacuated back to the RTO inlet for reprocessing. After purging, it will become an outlet bed. This occurs on a continuous basis. Like the puff capture, this option offers high destruction efficiencies, typically greater than 99% reduction in VOCs.
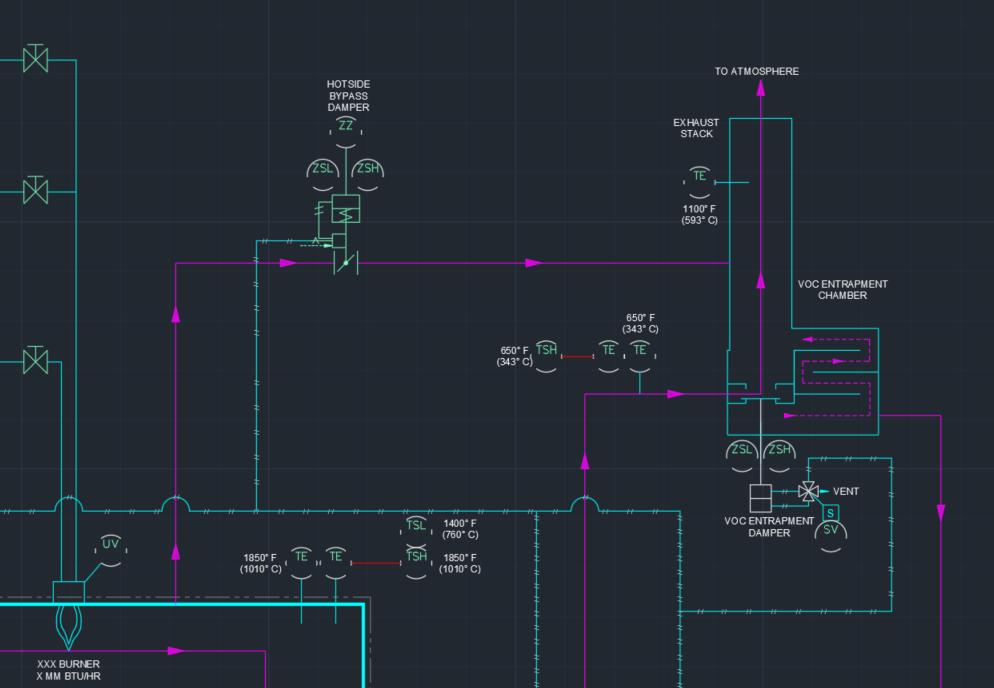
Custom Built Regenerative Thermal Oxidizer (RTO) Treating Food Packaging Emissions
Kono Kogs designed, fabricated & installed a custom RTO at a food packaging manufacturer
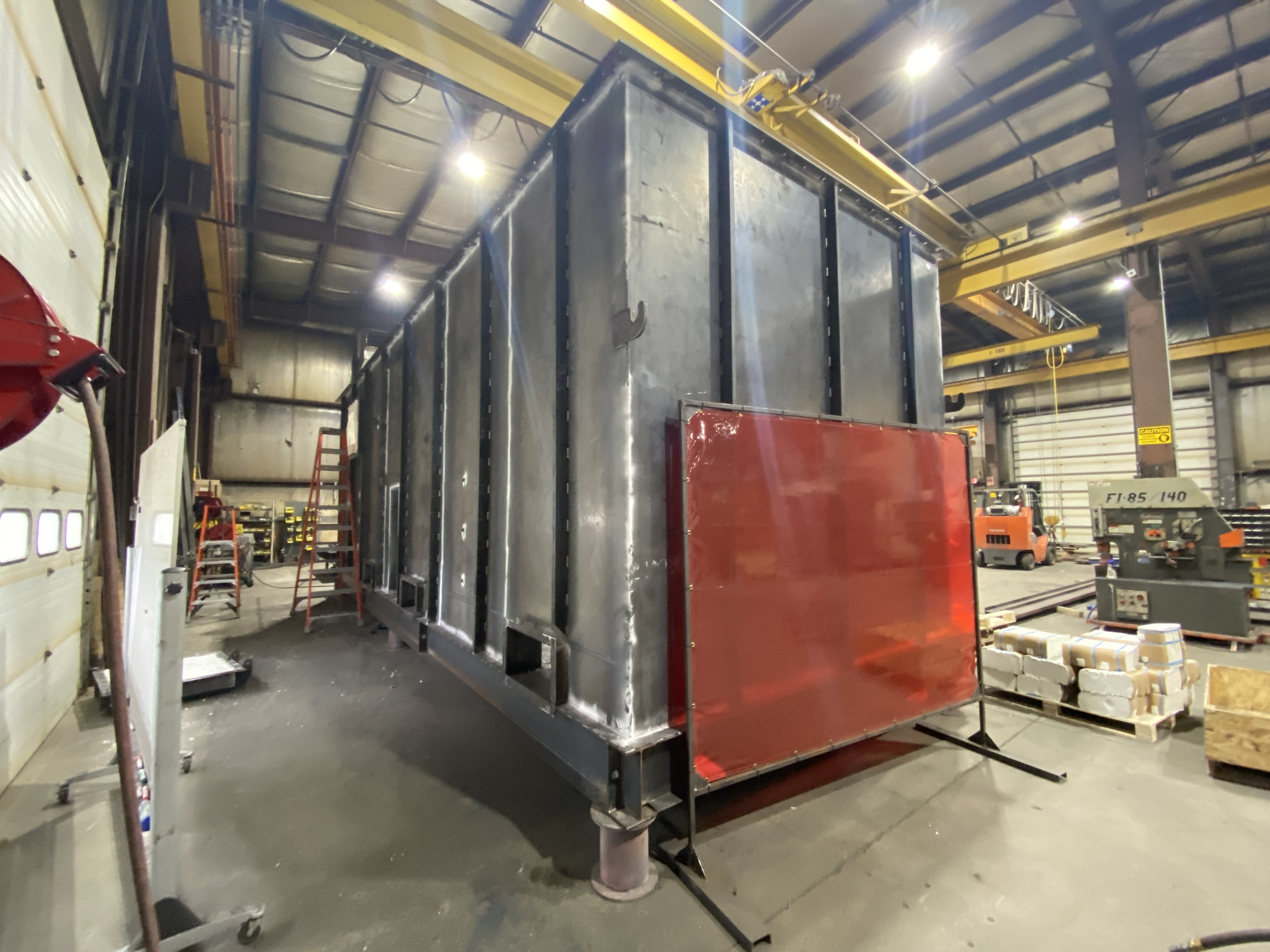
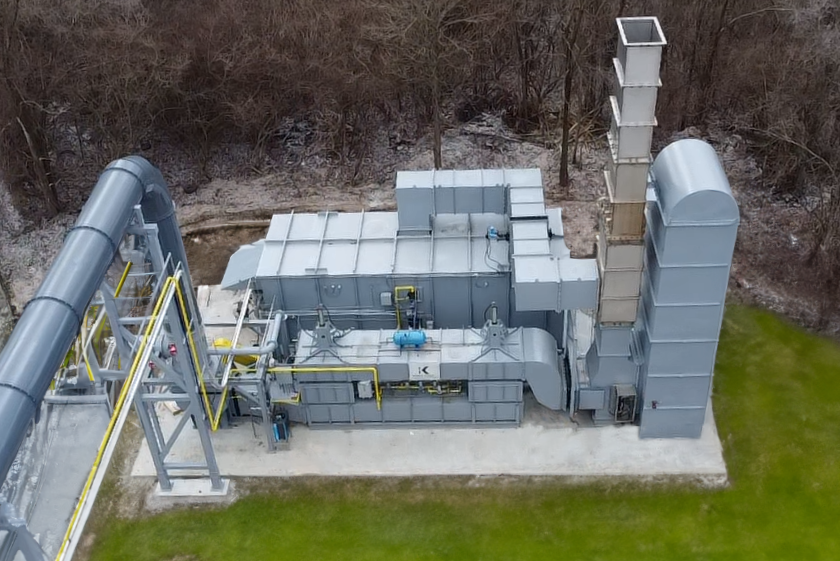