RTO Replacement or Refurbishment? Evaluating Your Regenerative Thermal Oxidizer
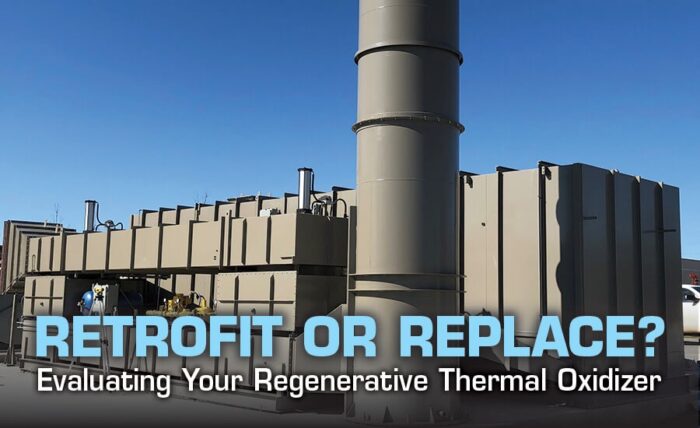
Replace or Refurbish Your RTO
In an article published in the February 2021 issue of Process Heating Magazine we discuss RTO replacement vs. on-site refurbishment options, and how to evaluate your unit. Enjoy the article below, and call us with any questions.
Do you have an aging regenerative thermal oxidizer (RTO) in your plant? Take a walk around it, and when you do, think back: Do you remember when you first saw it? Good-looking new paint, the latest PLC that responded speedily, and all the latest gadgets that shone like jewelry set it off against all the other RTOs in the neighborhood. Now, take another circuit around it, remembering all of your years of service together. Think about how you both suffered through some difficulties, but the RTO did its part and you did yours. You wonder, “Could it be like it was before?”
You might be considering a replacement, but you hesitate and ask: “Is this necessary, and do I really want to do this?” Your friend down the street thought the grass was greener, replaced his old RTO with a new one and, whew, was that costly! Conversely, the other company down the street just ignored theirs, and eventually it began routinely breaking down. The cost for the emergency surgeries would have gone a long way toward buying a new RTO.
Weighing the Alternatives
Before you jump the gun and dispose of your regenerative thermal oxidizer, consider your options. Are modern RTOs simply electrically enhanced versions of 20-year-old designs? Certainly, that is true about some.
What are the advantages of a new system? Rotary switching valves are nice, but functionally, poppet valves still are a proven design. In fact, most of the new RTOs sold still utilize pneumatically driven poppet valves.
A new oxidizer will incorporate the latest PLC technology. This will provide improved troubleshooting diagnostics as well as remote monitoring and troubleshooting capability via Ethernet. But, a new oxidizer is not needed to take advantage of the latest PLC capabilities: The newest PLC technology can be added to your existing RTO as well.
Modern thermal oxidizer systems typically have the latest ceramic media designs. These have made notable improvements in the last few decades. At the same time, new ceramic media combinations and designs can be retrofitted into your existing oxidizer, saving energy dollars and, most likely, providing up to 20 percent more airflow capacity.
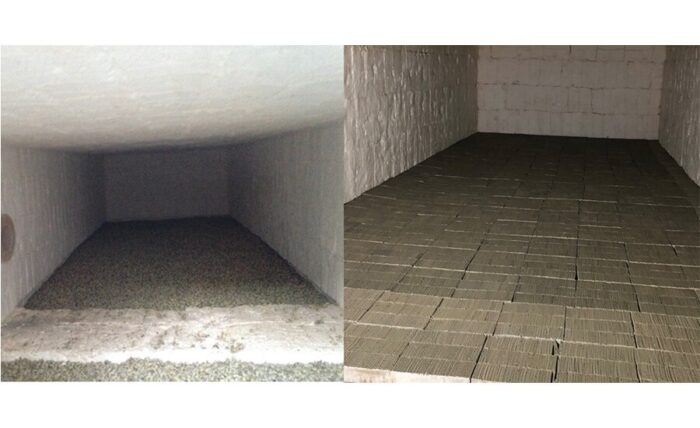
Choosing to replace a regenerative thermal oxidizer also involves other costs. They include removal and disposal of the existing oxidizer, shipping of the new system, the construction of a new concrete pad, any required modifications for ductwork, electrical wiring, and gas and air piping for tying in the new system, and a new air permit.
As an alternative to replacing your regenerative thermal oxidizer, consider what capabilities a field or shop rebuild could add. First, take an honest look at your RTO. How does it really appear? Does it still seem robust? Does it have “good bones”? Routine signs of age like cosmetic flaws and increased operating noise as leaks and bearings sound off can be addressed during a rebuild — as long as the metal and insulation are sound. With a retrofit, all of the subsystems can be updated on-site, and, if planned wisely, the rebuild can be completed with little downtime. In oxidizers with good mechanical integrity, a rebuild can significantly improve performance.
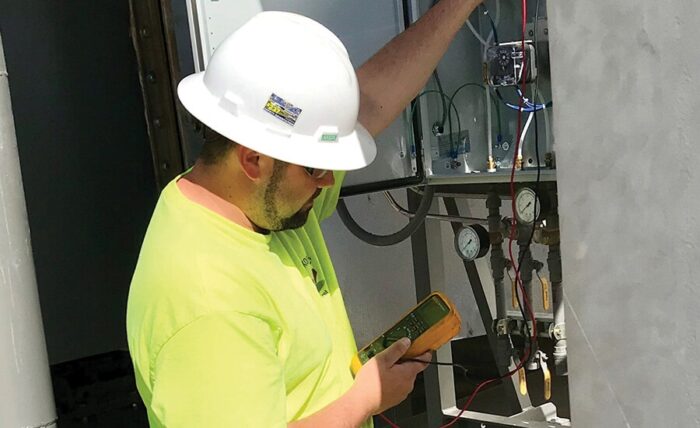
Preventive Maintenance and Upgrades to Consider
For many thermal processing systems, there is a time when replacement is unavoidable. If your regenerative thermal oxidizer system is aging but has not reached that point, it can be tuned and upgraded. A partial upgrade can provide 5 to 10 more years of service with significantly lower operating costs. A full upgrade could potentially provide another 20 years of service.
Here are some recommended preventive services to consider that will help you get more out of your existing oxidizer. They are listed from lowest to highest expected cost.
Burner Tuning
Burner and gas train technology has not changed much in 20 years, and fans are still fans, with no significant breakthroughs of late. Still, proper tuning is important. If you cannot recall the last time you had it done, the burner should be tuned. This will optimize burner output and ensure fuel is not wasted. A properly tuned burner helps protect ceramic media from flame impingement caused by poor flame definition. By contrast, a poorly tuned burner can waste a significant amount of fuel and, ultimately, money. In fact, an improperly tuned burner may even negatively impact the oxidizer’s VOC destruction performance.
Valve Tuning and Timing
Poppet valves or butterfly valves move fast, and poor timing can cause pressure pulses back to the process. This can lead to “oil-canning,” or visible waviness of the flat areas of the valve manifolds. Poor valve tuning and timing also can affect the process performance and negatively impact VOC destruction efficiency. Consider an inspection of all valves and dampers.
Repair Damaged Insulation
Hot spots are signs of issues with insulation integrity. Paint does not discolor on properly insulated metals. Hot spots should be inspected immediately to mitigate the chance of a more serious condition such as metal deformation and the creation of holes in the metal. These issues need to be dealt with quickly for personnel protection as well as RTO longevity.
Inspect Door and Valve Gaskets and Tighten Loose Dampers
Leaks and loose dampers will reduce both VOC destruction efficiency and thermal efficiency. Leaking door gaskets can provide an avenue for hot gases to find the atmosphere, causing an unsafe situation. In addition, such leaks likely will leave a mess on the door frames, especially if the solvents are the condensable type.
Optimize the Airflow from the Processes
As systems get older, process T-dampers loosen up and process variables change. This can negatively affect the expected airflow level from the process to the regenerative thermal oxidizer.
Another common problem occurs when the operators think the oxidizer is not pulling enough air. They may take it upon themselves to open the damper “just a little bit more.” Such adjustments can actually cause an airflow imbalance. For this reason, it is good practice to compare the original design specifications to the actual design airflow conditions periodically. Over-exhausting the process can increase fuel use while under-exhausting from a process can increase the required drying time and affect product quality.
Schedule a Service Call
Regenerative thermal oxidizer systems need inspection, tuning and even parts replacements periodically to ensure continued operation at peak performance. Some of the adjustments already mentioned such as burner tuning and insulation repairs can be addressed during a preventive maintenance (PM) service call. If they are not addressed on a routine PM schedule, these tasks may pop up as off-schedule emergency maintenance repairs, which are far from ideal and more costly. Being reactive rather than proactive throws production schedules off and could compromise your customer base. Service calls for preventive maintenance will serve you well over the years. Consider scheduling one, especially if it has been more than a year since the last PM visit.
Ceramic Media Replacements
Ceramic media technology has improved dramatically. New structured media designs can achieve 20 to 25 percent capacity increases compared to ceramic saddles with a simple replacement. The lower pressure drops and higher performance of structured media — products like multilayer media or extruded designs — can be retrofitted in round, oval and rectangular ceramic media beds. Of course, random packed (saddle-style) ceramic media are another good choice and, if properly designed, can reduce natural gas consumption and save on electrical costs by reducing fan horsepower.
Controls Upgrade
New PLC designs have significant processing power, something an RTO does not really need. But, a new PLC CPU provides key advantages such as reduced obsolescence concerns, improved troubleshooting with first-out fault and alarm logic, and Ethernet access via a remote station. When your staff cannot troubleshoot the issue, the oxidizer can be viewed remotely to assist with troubleshooting. Also, touchscreens are significantly improved over past designs, and it is possible to add supplemental touchscreens at each process control cabinet. Much of this work can be done offline, reducing oxidizer downtime.
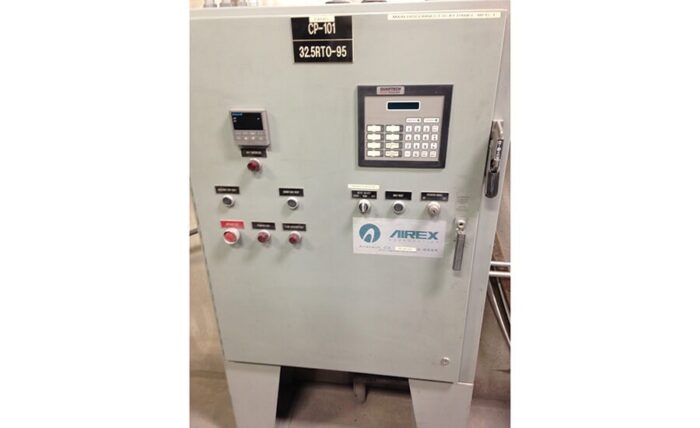
Secondary Heat Recovery
Regenerative thermal oxidizer systems offer the highest thermal efficiency of any oxidizer technology. This leads to low fuel costs to operate, which is the goal.
This also means the RTO exhaust temperature is low — about 100°F (55.6°C) warmer than the incoming process air temperature. Therefore, secondary heat recovery is often not cost effective. There might be sufficient heat available, however, if high VOC concentrations are expected, or the process exhaust temperatures are high. This heat can be sent back to the process or used elsewhere in the plant.
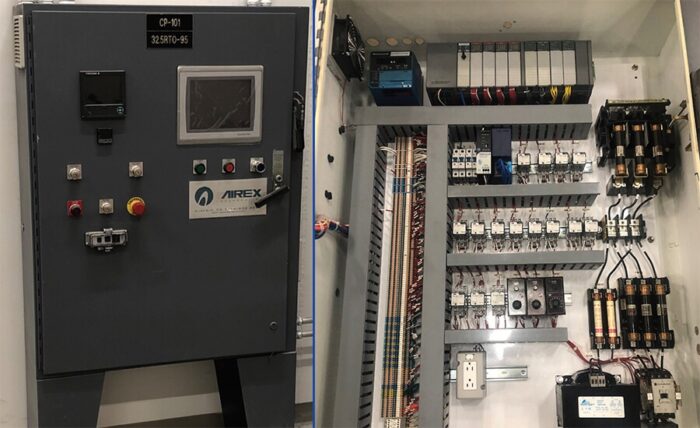
In conclusion, if you are considering a replacement or a rebuild of your existing regenerative thermal oxidizer, and an honest assessment shows it to be in good structural condition, you may benefit from a partial to full refurbishment of your existing system. The cost for the upgrades and refurbishing work will drive your decision, of course. Historically, refurbishing a well-built, solid-condition RTO on-site is a cost effective approach when compared to replacement, even when compared to a replacement with a used/refurbished RTO.
Considering RTO Replacement?
Kono Kogs is the world’s leading supplier of used oxidizer systems. Our core team has 150+ years of combined application and technical experience, and a 100% success rate meeting performance guarantees. We would very much like to help you find an economical solution to your emission control needs through oxidizer repair, upgrade or replacement. We’re happy to provide a free cost-benefit analysis for your application.
Call 920-432-2699 or contact us online with questions!
RTO Installation & Ductwork Treating Flexographic Printing Emissions
Kono Kogs refurbished & installed a second refurbished regenerative thermal oxidizer (RTO) for this major flexographic printer
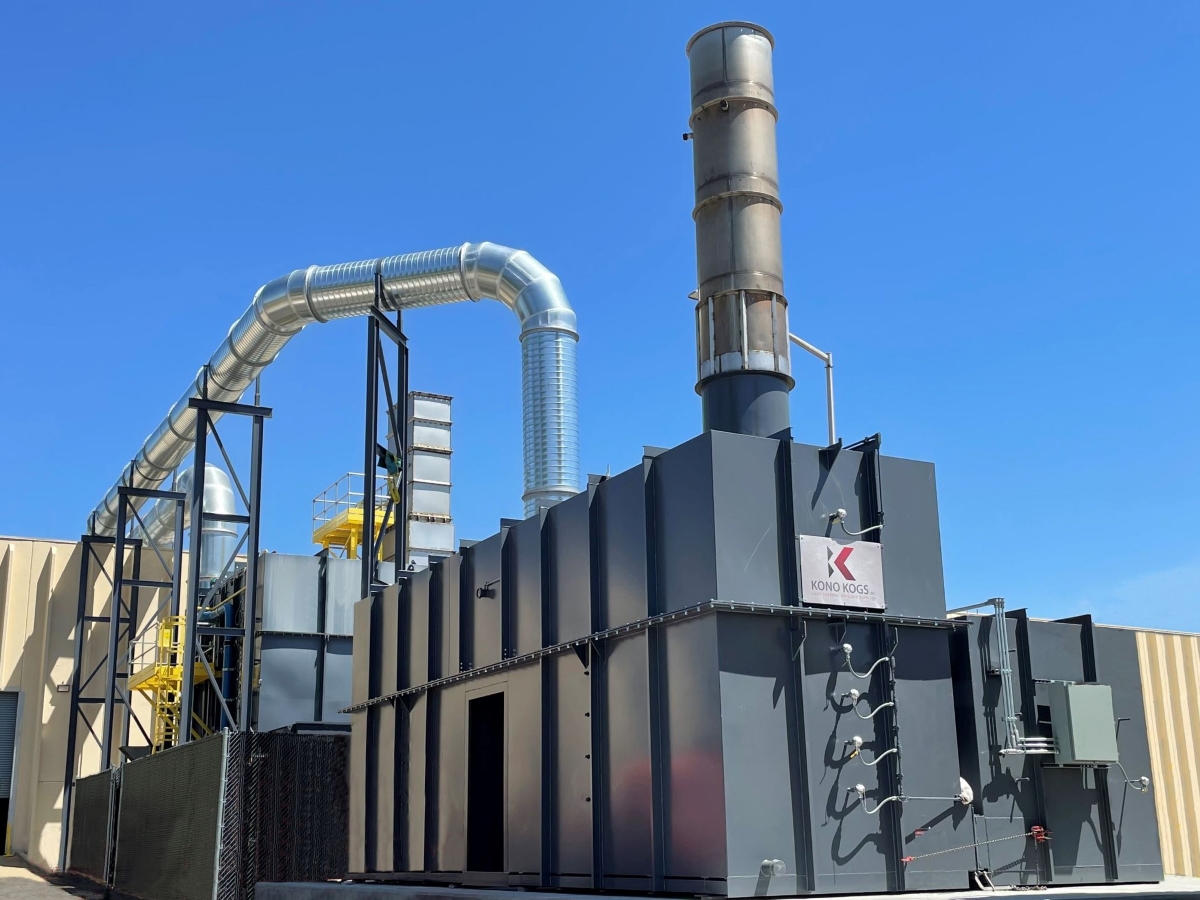