Regenerative Catalytic Oxidizers: What they are, what they do, and more
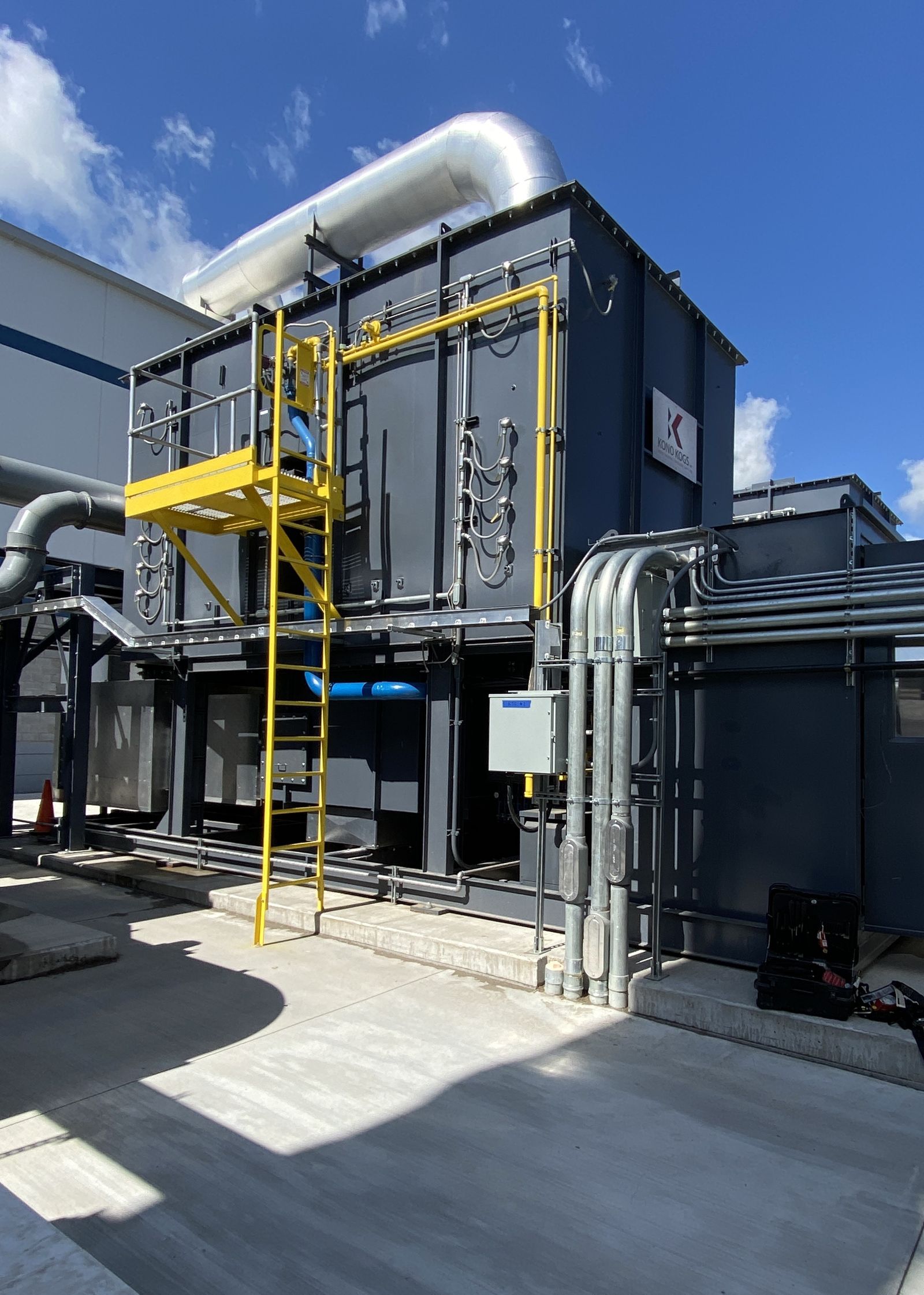
Learn about Controlling Air Pollution with Regenerative Catalytic Oxidizers
Our advanced regenerative catalytic oxidizers deliver exceptional efficiency and significantly reduce emissions, ensuring optimal performance and environmental compliance.
What is a Regenerative Catalytic Oxidizer?
Regenerative Catalytic Oxidizers (RCOs) are advanced air pollution control systems that combine the heat recovery features of Regenerative Thermal Oxidizers (RTOs) with the low operating temperatures of catalytic oxidizers. This combination results in the most energy efficient oxidation of volatile organic compounds (VOCs) and other pollutants. RCOs are significantly more energy efficient than other oxidizer technologies; even better than the extremely energy-efficient regenerative thermal oxidizer technology.
What They Do
Regenerative Catalytic Oxidizers convert harmful VOCs into carbon dioxide and water vapor, significantly reducing the environmental impact of industrial processes on the environment. One of the primary benefits of RCOs is their energy efficiency. The regenerative heat recovery process allows these systems to achieve thermal efficiencies of up to 95%, like an RTO, but at significantly lower operating temperature, which means they use less fuel and achieve lower operating costs.
How Does a Regenerative Catalytic Oxidizer Work?
A basic rundown of the operation process of an RCO includes:
- Preheating: The incoming polluted air is preheated by passing through a heat exchanger. This reduces the amount of additional energy required from the burner to reach the optimal temperature for the catalytic reaction.
- Combustion: The burner fires to drive the polluted air temperature in the combustion chamber up to the setpoint (750-850 F).
- Catalytic Reaction: The polluted air then passes through a catalyst bed where VOCs are oxidized at temperatures much lower than RTOs and thermal oxidizers.
- Heat Recovery: The hot, clean air exiting the catalyst bed gives off heat to the ceramic bed for use in preheating the incoming polluted air.
- Exhaust: The cleaned, cooled air, now free of VOCs and other pollutants, is released into the atmosphere.
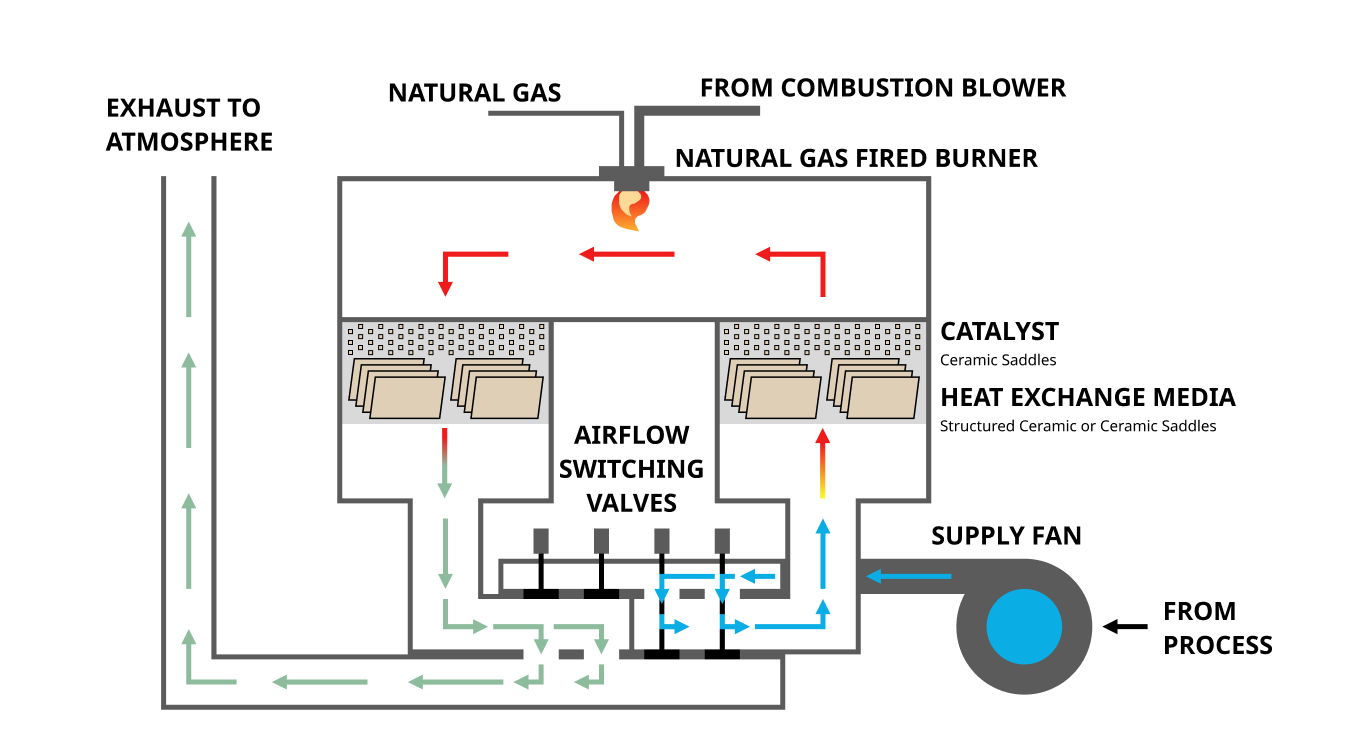
Benefits of Regenerative Catalytic Oxidizers
RCOs offer a range of benefits compared to other pollution control solutions, including:
Energy Efficiency
By far the greatest advantage of an RCO is it's energy efficiency, especially when VOC concentrations are low. By incorporating regenerative heat recovery at very low operating temperature, an RCO can operate at 40-50% fuel savings relative to an RTO; 80% savings relative to a recuperative catalytic oxidizer (CATOX), and 90% savings relative to a thermal oxidizer (TOX). This is achieved with electric operating cost comparable across all these technologies.
Lower Operating Temperatures
The catalytic process allows for oxidation of VOC/HAPs at much lower temperatures (750-850 F).
High Destruction Efficiency
RCOs can achieve VOC/HAP destruction efficiencies of up to 99%, offering compliance with most environmental regulations.
Operation as an RTO
Nearly all RCOs are designed to also operate as RTOs with only some simple logic changes. This is helpful, if process changes are needed for any reason in the future, but the changes could harm catalyst. An RCO can be easily converted to operate as an RTO.
Limitations of Regenerative Catalytic Oxidizers
While there are many benefits to incorporating an RCO into a pollution control process, there are some limitations to be aware of, including:
Low Versatility
Due to the risk of catalyst poisoning and masking, RCOs are not compatible with some industrial applications. Common poisons are halogens. Common masking agents are silicone and phosphorus. Also, future changes to your manufacturing process may be hindered if an RCO system is in place.
Catalyst Replacement Cost
When catalyst is poisoned, RCO performance can rapidly drop, requiring potentially costly replacement. It is important to know your process conditions to avoid unexpected catalyst replacement cost.
Catalyst Testing Cost
Catalyst must be tested periodically to ensure proper performance, per most operating permits. This has some additional costs, but are typically greatly outweighed by the fuel savings realized with an RCO.
Future Process Changes are Restricted
A process change that is identified that would improve product throughput or differentiation, or some other benefit, may be hindered from consideration if it might introduce catalyst poisons. If process changes are anticipated, be sure to let your oxidizer supplier know prior to committing to an RCO system, or introducing it to an existing RCO.
Applications of Regenerative Catalytic Oxidizers
Dozens of industries may be using RCOs as a pollution abatement solution, but some of the top ones include:
- Chemical Manufacturing
- Rubber & Latex
- Pharmaceuticals
- Wood Products
Maintenance and Operation
Maintaining RCOs involves regular inspections to ensure the catalyst is functioning properly. Over time, the catalyst may need to be replaced to maintain VOC destruction efficiency. Continuous monitoring of system performance helps in early detection of issues and ensures optimal operation. Advanced control systems provide real-time data on the performance of the RCO, allowing for proactive maintenance.
Regenerative Catalytic Oxidizers offer a highly efficient and cost-effective solution for controlling air pollution. By combining the benefits of regenerative heat recovery and catalytic oxidation, RCOs provide superior performance in a variety of industrial applications. Their ability to achieve high destruction efficiencies at lower operating temperatures makes them an attractive option for industries looking to reduce their environmental impact while maintaining operational efficiency.
RTO to RCO Retrofit
It may be possible to retrofit catalyst in your existing RTO system to realize the significant fuel savings of an RCO. There are continual advances in catalyst technology opening up more industrial applications for treatment with an RCO. Fuel savings of 50% is possible in many applications. Some even achieve self-sustaining (no fuel use) during normal operation because there is enough VOC concentration in the airstream. Let us know your process details and we can propose the best solution for you. Even if your process is not a match for an RCO, we can also review the benefits of replacement of your ceramic media to achieve both lower fuel and electric cost.
Common Questions about Regenerative Catalytic Oxidizers
Get quick answers to some of the top questions we receive about RCOs here:
Yes. It is normally a simple conversion.
Your operating permit will define a time (typically every 5 years), but a wise maintenance practice is to test annually as part of a preventive maintenance inspection.
RCOs offer greatest fuel economy by far, while recuperative units may be best for high VOC concentration airstreams (or an RTO can be considered).
Chemical, pharmaceutical, OSB (oriented strand board) press, particle board dryer, MDF (medium density fiberboard) dryer, plywood, paint spray booths; and any application under 2% LFL is a good candidate
In most cases, yes. But proper evaluation is recommended to establish that no potential catalyst poisons or masking agents are present in your airstream.
Extensive catalyst application experience allows our engineers to select the best catalyst type, and pair it with an optimized ceramic media mix for long life, and for low fuel and electric use.
Chemical, pharmaceutical, and wood products.
Ceramic Media Upgrade for Automotive Paint Line
Proper RTO ceramic media bed design for an automotive manufacturer's spray booth emissions helped this customer greatly reduce plugging issues from their siloxane solids.
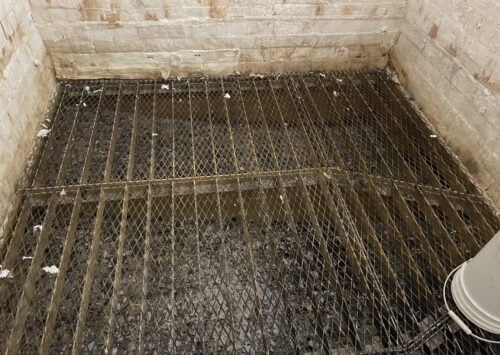
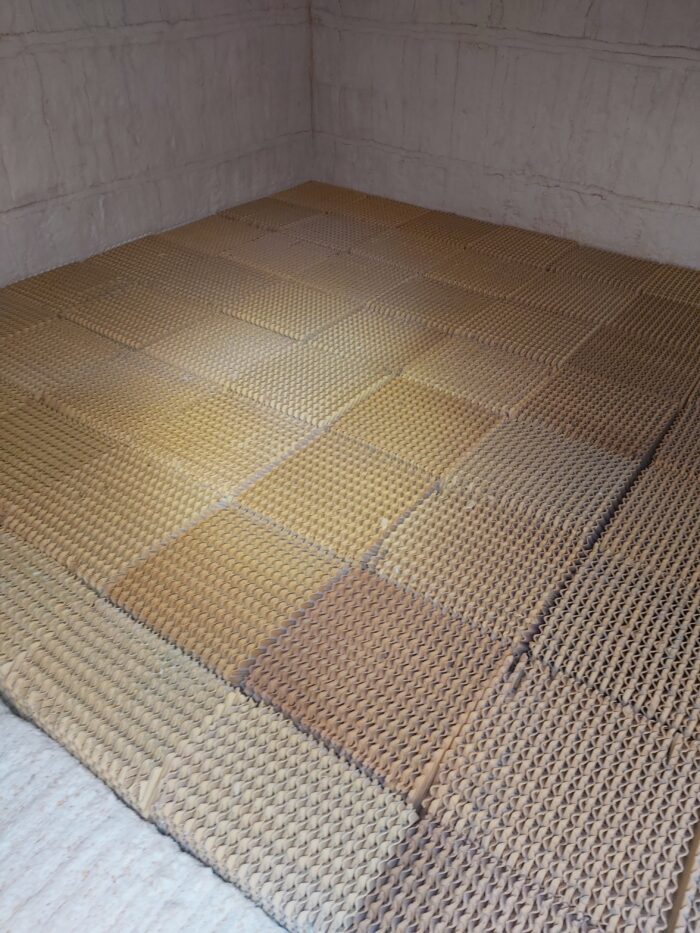