What is the Difference Between a Regenerative Catalytic Oxidizer and a Recuperative Catalytic Oxidizer?
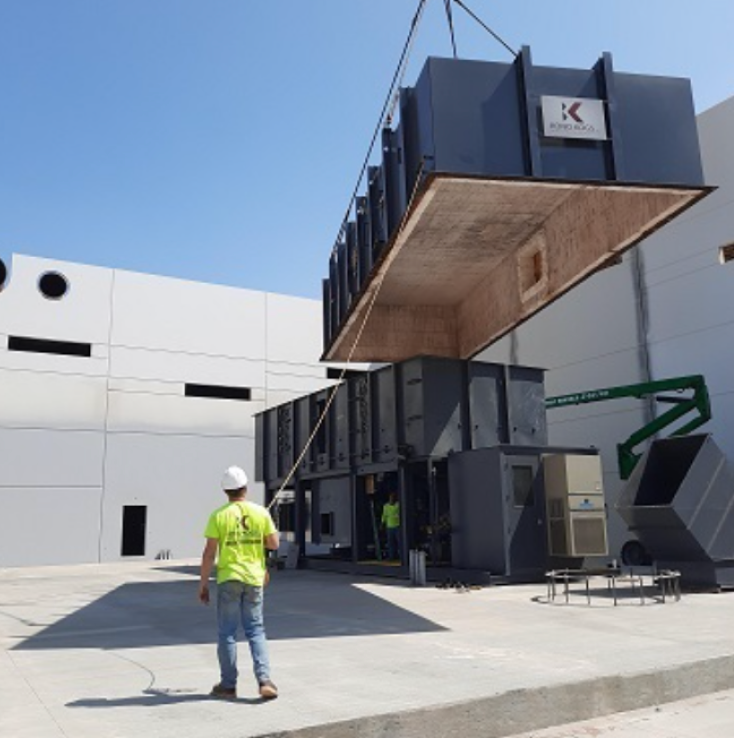
RCO vs CATOX
While both are a type of catalytic oxidizer, the difference between a Regenerative Catalytic Oxidizer (RCO) and Recuperative Catalytic Oxidizer (CATOX) is how these machines recover heat to reduce fuel demand in the oxidation process.
A RCO utilizes multiple ceramic media beds as a heat exchanger, while a CATOX utilizes a metal heat exchanger to recover heat. Each technology destroys pollutants by heating the dirty airstream up to a setpoint temperature. The heated airstream then passes through a catalyst bed to and the VOC/HAP is oxidized and converted to carbon dioxide and water vapor. The method of heat exchange is significantly different between the two systems. Let’s compare the two type.….
Recuperative Catalytic Oxidizer (CATOX) Basics
A CATOX uses a familiar air-to-air metal heat exchanger to recover heat from the hot, cleaned air before it is exhausted to atmosphere. The recovered heat is used to pre-heat incoming, dirty air. This pre-heated air then is heated by the burner to a setpoint temperature (typically 600-650F). This air -at setpoint temperature- is then passed through a catalyst bed where VOC/HAPs are oxidized and converted to carbon dioxide and water vapor before passing through the hot pass of the heat exchanger. The cooled, clean air is then exhausted to atmosphere. The heat recovery efficiency is typically around 70% but customized for the application from 0% to 80+%. One major difference is that the airflow in a CATOX is in one direction, continually.
The benefit of using a CATOX is high VOC destruction (up to 99%) at low operating costs.
Get more detail on thermal recuperative oxidizers.
Regenerative Catalytic Oxidizer (RCO) Basics
A RCO is much more complicated in operation. A regenerative heat exchanger, by design, is much more energy efficient than a recuperative heat exchanger. Regenerative heat exchangers utilize airflow reversals, and two ceramic heat sinks (beds) to absorb and give off heat, and control logic to make it all work - achieving very high thermal efficiency. The exiting bed of the RTO absorbs heat from hot, cleaned air before it exhausts to atmosphere. The heat stored in this bed releases to the dirty cool air passing over it in the next half cycle, pre-heating this air before it enters the combustion chamber. This pre-heated air is then passed through the combustion chamber, brought to setpoint temperature (750-850F), passed through the catalyst bed where VOCs are oxidized before exhausting to the atmosphere. One major difference is that the airflow in a RCO reverses direction approximately every 2-3 minutes.
Get more detail on regenerative thermal oxidizers.
Recuperative Catalytic Oxidizer (CATOX) or Regenerative Catalytic Oxidizer (RCO)– Which is Better?
RCOs save significantly in fuel use (80% savings) compared to CATOX units. RCOs are typically more expensive than CATOX units, but for low VOC concentrations the fuel savings quickly justifies the RCO. However, CATOX units are much lighter than RCOs so they are well suited for roof mounted applications. VOC concentration would determine the best system for any application where catalyst technology would be a good match. For higher VOC concentration airstream (>4% LFL) you may also want to consider an RTO. These do not have the inherent risks of catalyst poisoning or limiting your process flexibility possible with catalytic technology.
Give us call to discuss your particular application, or request a quote.
For more detailed comparison of oxidizer technologies click here: Selecting an Oxidizer
Catalytic Oxidizer Treating Foil Coating Emissions
Start-up company needed emission control with low capital & operating costs. We recommended a 12,000 scfm catalytic recuperative oxidizer with bead catalyst.
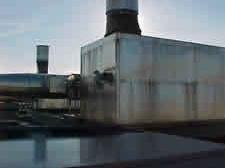