Repairing your Recuperative Thermal Oxidizer
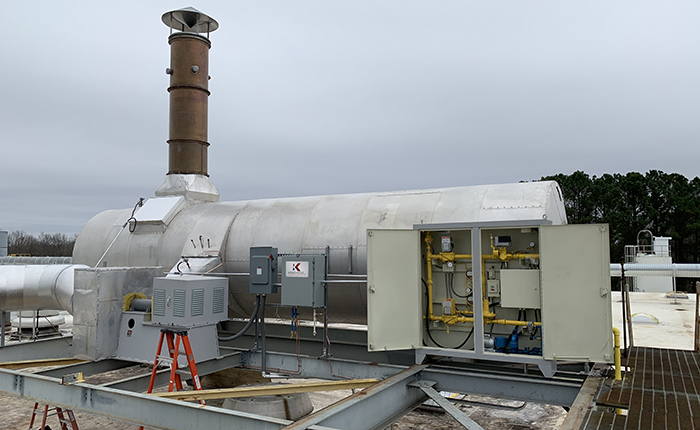
Troubleshoot & Repair your Recuperative Thermal Oxidizer
From one-time problems, to lingering problems that have baffled you or your OEM, we have seen and repaired nearly every oxidizer issue
Repairing your recuperative thermal oxidizer is no small investment, so performing routine oxidizer maintenance is an important part of keeping your pollution control system operating efficiently and effectively. Regularly scheduled inspections by both your staff and our technicians will prevent costly repairs and downtime of your system.
However, even with regular inspections, breakdowns happen. Our expert team at Kono Kogs can help troubleshoot and repair your thermal oxidizer 24/7 365 days a year. We have created the troubleshooting below that will give you a place to start.
Troubleshooting Guide
Download Troubleshooting Guide PDF
If you are unable to solve your issue by using the trouble shooting guide, below are a few less common thermal oxidizer repairs that our company deals with on a more regular basis.
Four Things to Check When Repairing Your Recuperative Thermal Oxidizer
Below are a handful of items to check when you're repairing a recuperative thermal oxidizer.
Heat exchanger/economizer issues
The heart of a recuperative thermal oxidizer is the heat exchanger. Plugging or cracking are common problems that may result in increased gas use. They may also cause the oxidizer to fall short of its destruction efficiency, leading to increased downtime. Cracks in the plate or shell/tube of the heat exchanger provide a path for dirty air to short circuit to the exhaust stack thereby allowing cross-contamination of the clean and dirty air. Due to the thin walls typical in a plate heat exchanger, repair is not usually practical or possible and will require a complete replacement.
Shell and tube type exchangers typically are constructed of components and because of this are better candidates for repair, depending upon the crack location. Plugging may require flushing or vacuuming to return to the original flow capacity. Photos of the heat exchanger cracks and their locations, or information on the nature of the material causing the plugging, will help us determine the best solution. Give us a call we can help.
Insulation hot spots
Due to the high operating temperature of these systems, hot spots are common. Paint discoloration is the first sign of a problem and metal deformity and rust spots point to a more concerning issue. Thermal oxidizers usually operate at positive pressure so hot spots can breach due to metal oxidation eventually releasing hot air outside to the atmosphere. This condition will need immediate repair to protect the system, as well as your personnel. Our team can provide guidance to identify the problem and repair the hot spot and insulation. We also dispatch our team quickly for repairs if help is needed. Give us a call and send photos for the fastest support.
Exhaust stack test failure
Thermal oxidizer repairs to address a failed exhaust stack test might include inspecting the heat exchanger (see note above). Strategic placement of sensors when the testing agency is still on site can help identify the source of the problem. It may be due to a crack in the heat exchanger or poor burner set-up resulting in undesirable products of combustion.
Also, poor flow characteristics due to heat exchanger plugging could reduce dwell time in the unit; this is one of the primary criteria that must be met to ensure the conversion of the VOC to CO² and water vapor. If you can reach us when the testing firm is still on site, we can direct the troubleshooting and assist with determining a solution. Even if the testing agency has left, our team can still review test data and the testing protocol to help narrow down the source of the poor performance.
Pneumatic actuator freeze up
This is one of the most common early winter RTO problems. Many oxidizer systems utilize pneumatic actuators which work well if compressed air dryers are operating properly. Any hiccup in the air dryer operation during the year can result in lingering moisture in the air lines when the cold weather arrives and the moisture freezes.
A common location affected are the ports in the actuator solenoid valve, effectively locking up the actuator, causing an oxidizer fault. To correct this problem is typically a tedious task involving tracing lines and devices with heat tape, using heat guns to thaw ice, and weather shields (blankets, etc.) to protect critical components. Give us a call and we can tell you what works best.
To avoid this problem before it starts follow these steps:
- Purge your air lines especially at the low spots and the furthest point from the air dryer.
- Install a dessicant dryer. A dessicant style is the best air dryer technology available and we recommend -40⁰ F dew point desiccant but have also used -100⁰ F dessicant in some applications.
- Be sure to service your air dryer per the OEM guidelines. Desiccant can foul over time due to poor air filtering. Desiccant is inexpensive, so replace it as often (or more) as your OEM specifies. A maintenance agreement with a compressed air service firm keeps the dryer in focus and running properly.
You may want to consider upgrading the rotary valve drive from pneumatic to electric, which can address the recurring issues experienced with the pneumatic valve drive design.
Still Looking for Air Pollution Control Equipment Repair Solutions?
We could list many more repair scenarios, but if your thermal oxidizer repair needs did not make the troubleshooting table or the list above, give us a call with your challenge. We have likely seen the problem and know the solution.
You May Need To Consider Long Term Solutions
Together we may ultimately discover that the repairs will only buy time, with no permanent, viable, economically reasonable solution possible. If a replacement oxidizer is needed FAST—and in an emergency that is usually the case—we have the world’s largest inventory of quality used thermal oxidizer systems. Many of our oxidizers are ready to ship immediately! We can configure them to match nearly every process flow rate and solvent mix, and expedite delivery to get you operational as soon as possible.
If we have been helping you with the repair we may already know all we need to know to propose an alternative to your current oxidizer. Though this may be a larger capital outlay than a simple repair, the new technology we offer will always result in fuel and electric savings with HIGHER RELIABILITY, allowing you to return your focus to what you do best.
Depend on Kono Kogs for Emergency Repairs
At Kono Kogs, we want to be a resource for repairing your thermal oxidizer. Expert guidance will get it done right the first time. Getting your system back on-line is our top priority. After that we can consider any short-term solutions to keep you running into the future or possibly a long-term solution.
Let us help! Whether it’s 2 a.m. Saturday morning or first thing Monday, we are available to help with your emergency thermal oxidizer repairs. Call us at 920-615-8804.
MEGTEC Catalytic Oxidizer Treating Metal Decorating Emissions
A 3 piece can maker replaced an aging catalytic oxidizer with a higher capacity catalytic recuperative oxidizer (catox) for their wicket oven. The solution provided had exceptionally low capital cost compared to new equipment, allowed increased process line speed, and now (in 2024) has provided over 20 years of reliable performance.
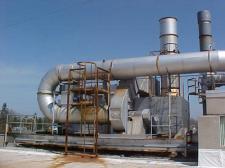