Emission Testing for Thermal Oxidizers
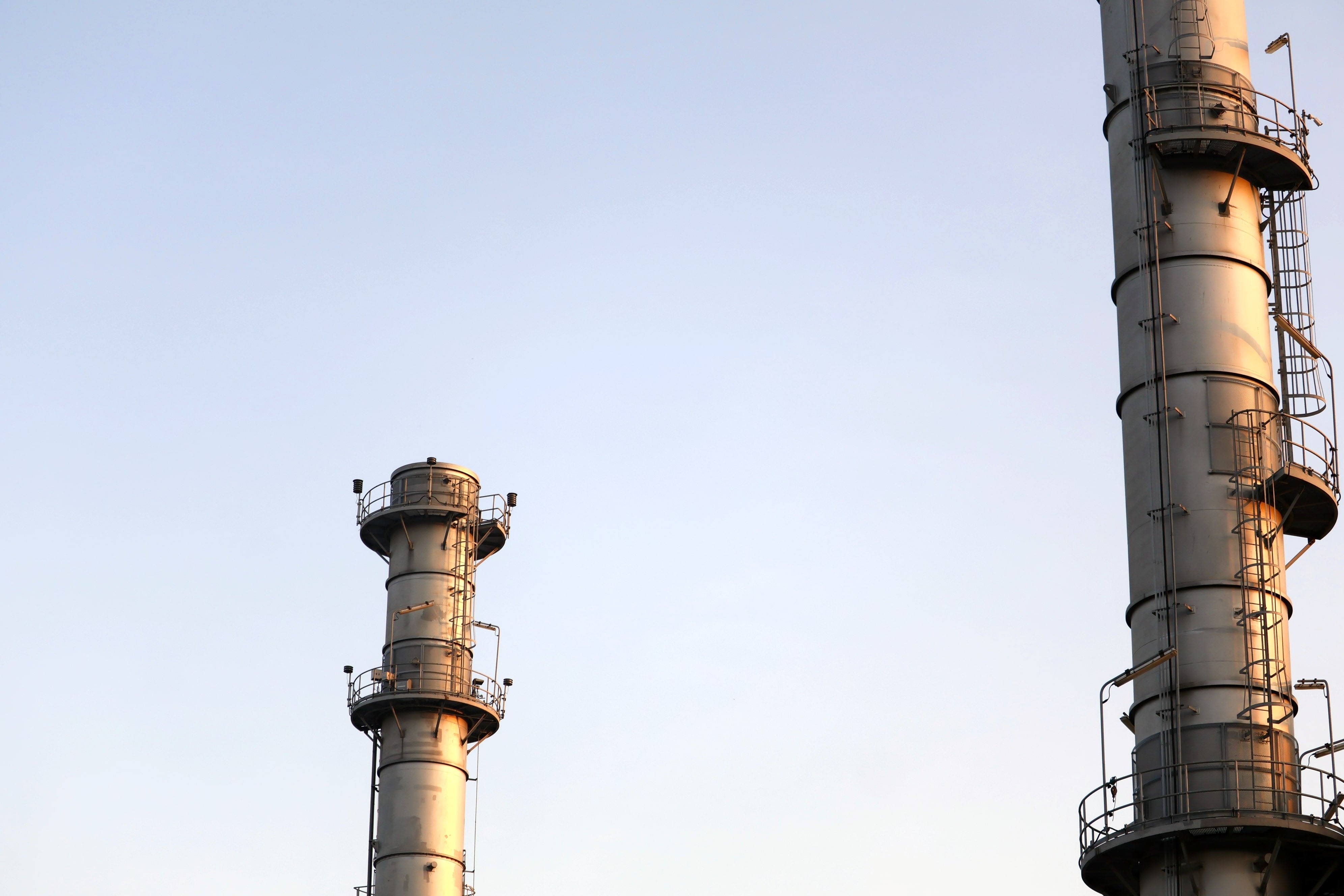
Verifying Thermal Oxidizer Performance through Stack Emission Testing
Ensure efficiency, compliance, and sustainability by regularly testing and monitoring your oxidizer system.
Emission Testing for Thermal Oxidizers
Performing emissions testing on a thermal oxidizer is essential to ensure it operates efficiently and complies with environmental regulations. Regular emissions testing helps ensure that thermal oxidizers operate within regulatory limits and reduce overall environmental impact, while protecting the investment in your pollution control system.
How to Perform Emissions Testing on a Thermal Oxidizer
Here are the key steps in the testing process:
Preparation:
- Perform a Preventive Maintenance Inspection of Your Oxidizer: Months before the test you may want to schedule a preventive maintenance service call to ensure the oxidizer is functioning properly.
- Identify Testing Parameters: Determine which pollutants need to be measured: VOCs, CO, NOx, and particulate matter.
- Select Testing Method: Select the appropriate test method for your emissions per your operating permit. Method 25A is the most common method for thermal oxidizers, and allows (near) real-time evaluation of results, and, if necessary, on-site troubleshooting of any problem identified.
- Review Test Protocol: Testing firms must develop testing protocols; be sure to review them with your oxidizer supplier. This will to ensure the test protocol matches the pollutants and the oxidizer technology being tested. For example, the correct sampling frequency is critical for RTO testing due to the nature of RTO operation.
- Select Testing Equipment: Use appropriate analyzers, calibration gases and sampling equipment for the pollutants being measured and the expected concentration of pollutants. For example, condensable solvents will require heated sample lines to accurately capture emission values.
- Calibrate Instruments: Ensure all testing instruments are calibrated according to the manufacturer’s specifications and regulatory requirements.
- Agree on Sampling Locations: Identify the points in the exhaust system where samples will be collected, typically at the inlet and outlet of the thermal oxidizer. Thermal oxidizers may be drawing from multiple process exhaust points routed to a single ductwork header. Be sure to find a laminar flow location with all process airstreams sufficiently mixed.
- Set a testing date: Keep in mind that if specific conditions are required/desired for your testing protocol, you may have to adjust your production plan accordingly. Also, set-up of the test will typically require access to the oxidizer 1 day before the test and tear down will require another day after the test completion.
Additional Sampling:
- Collect Comparative Samples: If methane is generated in the process being treated, be sure to isolate it for analysis. Bag sampling is the typical method for this.
Analysis:
- Evaluate Results: Many protocols require multiple tests (typically 3 that are cumulative) to verify performance. Having results immediately upon test completion allows on-site troubleshooting before testing equipment is taken down. Method 25A is typical for all thermal oxidizers, which allows this real time evaluation. This can avoid costly redeployment & set-up for an additional, future test.
- Record Data: Document the results, including the concentration of each pollutant, the operating conditions of the thermal oxidizer, and any deviations from standard procedures.
Reporting:
- Prepare Reports: Compile the test results into a comprehensive report that includes all relevant data, analysis methods, and compliance status.
- Submit to Authorities: Submit the report to the appropriate regulatory agencies as required.
Review and Action:
- Evaluate Performance: Assess the performance of the thermal oxidizer based on the test results. Identify any areas where emissions exceed permissible limits.
- Implement Improvements: Make necessary adjustments to the thermal oxidizer’s operation or perform corrective maintenance to improve efficiency and reduce emissions. See some common sources of stack test failures here. This is best accomplished while the testing equipment is still in place, allowing verification of performance improvements.
Need Help? Contact our team to learn more about executing an emissions test for your thermal oxidation system.
Common Questions about Thermal Oxidizer Emissions Testing
Find answers to frequently asked questions about emissions and emission testing for thermal oxidizers.
A puff capture feature can help eliminate visible emissions
Yes we can come out and help to determine what the problem is. Whether it be switching valves leaking; a leaking heat exchanger; poor air flow distribution; or poor catalyst performance. We can do a thorough evaluation and provide a turnkey solution in a short period of time and help to keep you in operation. If your system is a regenerative thermal oxidizer (RTO) see this blog post about stack test failures for more details on troubleshooting your RTO and test method.
We can come in and evaluate the current system by taking flows and readings at certain points of the system. Then we can determine whether the current system is optimized. If it isn’t we can recommend how to do that. If area capture hoods or enclosures need to be added we can recommend that as an option as well. We can also provide these things on a new system.
Treating Metal Decorating Emissions with a Dual Regenerative Thermal Oxidizer
See how Kono Kogs helped this company meet their air pollution control regulations with a turnkey solution that included a refurbished RTO.
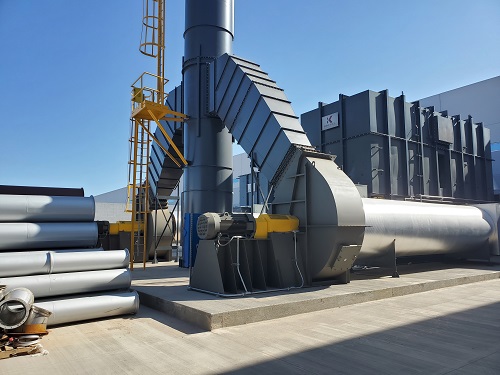