What Are VOCs, and What is Industrial VOC Removal?
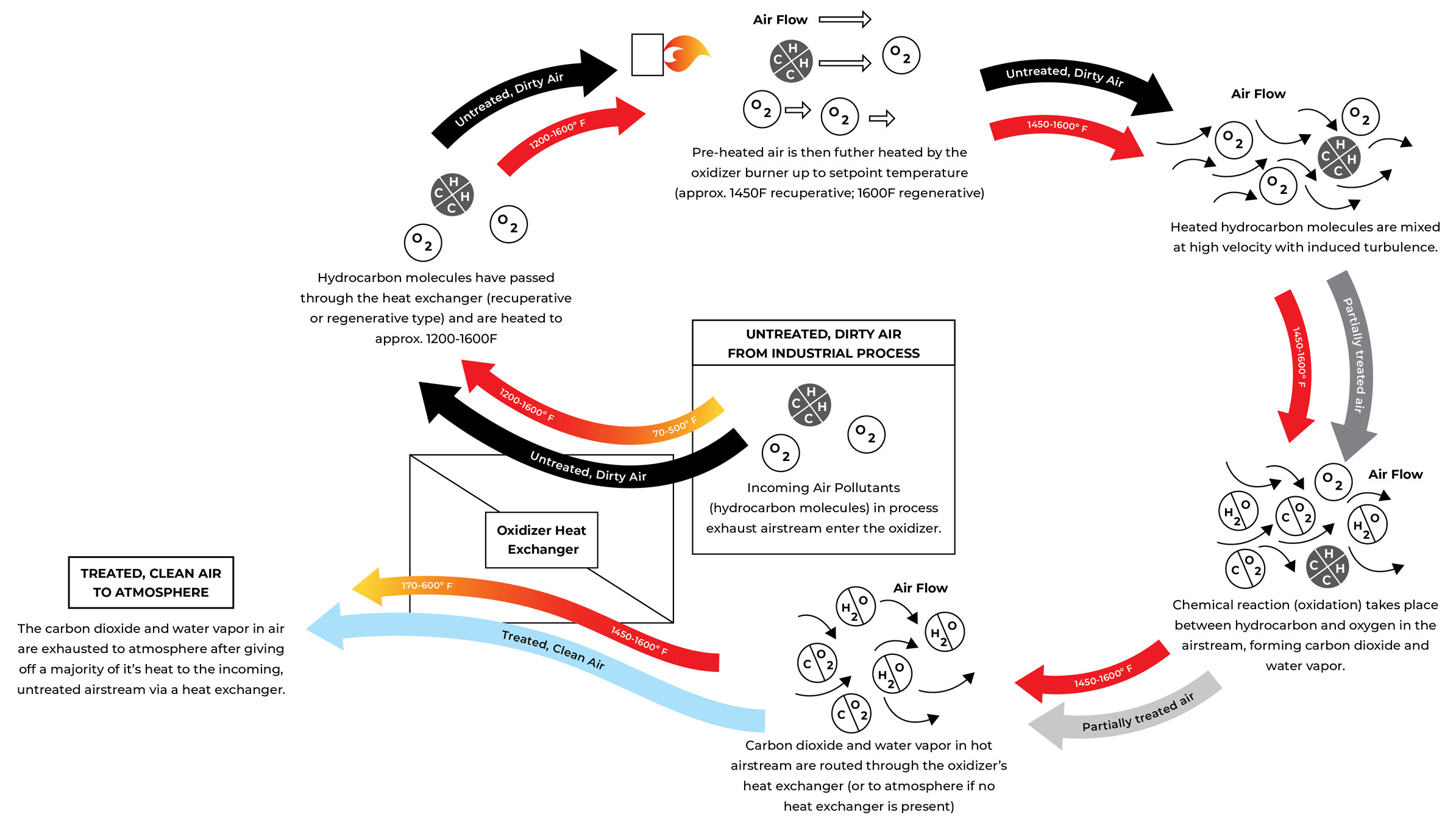
Industrial Volatile Organic Compounds & Their Removal
VOC removal from industrial exhaust airstreams is commonly accomplished by oxidizing hydrocarbons to form CO2 and water vapor before the airstream is exhausted to the atmosphere. Oxidation is accomplished with thermal oxidizer systems which have been proven to be a reliable VOC removal solution for decades.
What are Volatile Organic Compounds (VOCs)?
The term Volatile Organic Compound (VOC) refers to a broad range of chemicals. VOCs contain carbon, which makes them organic compounds. They can be further classified as hydrocarbons, aromatics, and aldehydes, and ketones. Each classification has specific properties which make them effective for their intended use, but also determines their environmental impact.
VOC Emissions Sources
VOCs are necessary compounds used in industrial manufacturing processes, found in household chemicals, or are byproducts of exhaust from automobiles, aircraft, and small engines. They can be harmful to the environment and to people, and can cause irritation of the eyes, nose, and throat, cause severe headaches, dizziness, shortness of breath, memory impairment, and even some cancers. VOCs that get released into the environment can react with nitric oxidizes creating smog emissions that can worsen when exposed to natural sunlight.
VOC Regulations At U.S. Federal Level
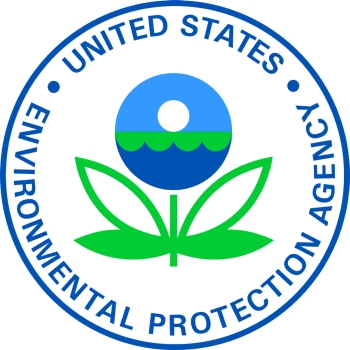
The U.S. EPA regulates VOCs at Federal level in 40 CFR 59, which stands for the National Volatile Organic Compound Emission Standards For Consumer And Commercial Products. This regulation provides guidance on the control and limits of specific VOC compounds for specific industries. The individual states impose limits for industries in their state or county or community based on where the community is located. There are also attainment and non-attainment areas within the USA that determine the strictness of regulations on a particular facility. All of these factors determine the tonnage of emissions allowed from each facility before VOC treatment systems, such as thermal oxidizers, must be added. Industries that have regulations in place include:
- Aerosol Can Coatings
- Architectural Coatings
- Automobile Refinish Coatings
- Coil Coatings – See Case Study
- Spray Dryers – See Case Study
- Aerospace parts
- Bakeries
- Chemicals
- Circuit Board Mfg.
- Coating & Laminating
- Coffee Roasting
- Electronics Mfg.
- Expanded polystyrene
- Fabric coating
- Fiberglass Products
- Flexographic Printing
- Graphic Arts Printing (Heat set web offset)
- Insulation Manufacturers
- Odor Control
- Learn more about the Industries Kono Kogs Serves here.
How Catalytic or Thermal Oxidizers Remove VOCs
A Thermal Oxidizer (often referred to as TOX, incinerator, or afterburner) destroys pollutants like Hazardous Air Pollutants (HAPs), Volatile Organic Compounds (VOCs), and odorous emissions that are often discharged during industrial processes safely and efficiently.
Industrial oxidizers achieve very high VOC destruction efficiency by heating and maintaining a polluted airstream at high temperature for a set dwell time. Typical VOC destruction is 99+%. Thermal oxidizers can operate with an integral heat exchanger for fuel savings or without for capital cost savings. All oxidizer technologies achieve VOC destruction by exposing pollutant-containing air to a high temperature, for a set period of time, in a turbulent flow path.
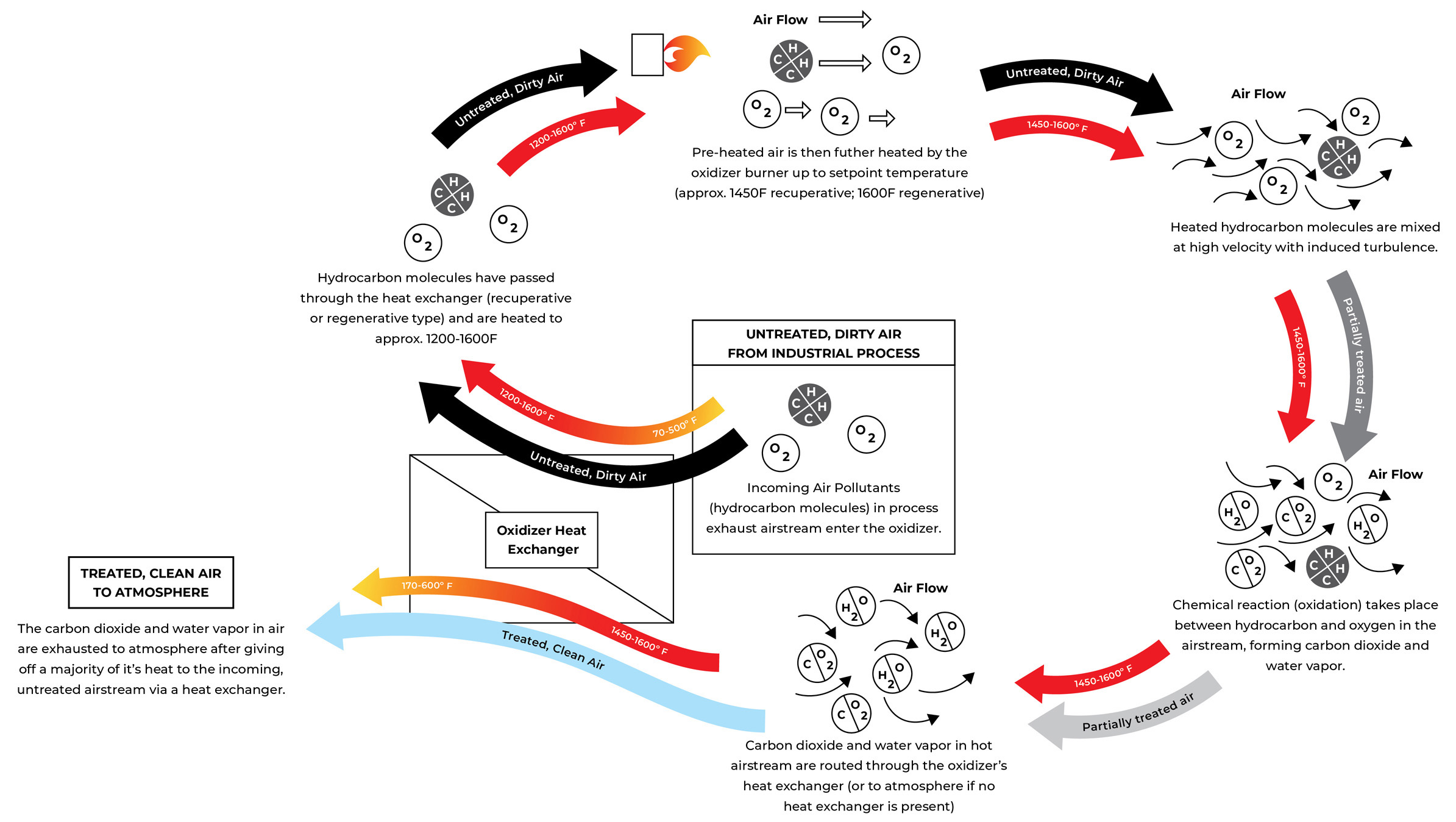
Industrial VOC abatement technologies
There are several different technologies available to remove industrial VOCs. Choosing the optimal VOC treatment system depends on the particulars of each application, such as amount of air to be treated, temperature of the airstream, the VOC types and subsequent concentration, and the required destruction rate efficiency (DRE). Real estate can also factor into your decision as different technologies have different footprints and weights.
Regenerative Thermal Oxidizers (RTOs)
One of today’s most widely accepted air pollution control technologies across industry is a Regenerative Thermal Oxidizer, commonly referred to as an RTO. They are very versatile and extremely efficient – heat recovery efficiency can reach 97%. This is achieved through the storage of heat by dense ceramic stoneware. Regenerative Thermal Oxidizers are ideal for airstreams with low VOC concentrations with high operating hours each year.
Thermal Recuperative Oxidizers
A less popular thermal oxidizer technology is a recuperative oxidizer. Thermal recuperative oxidizers have an integral heat exchanger which preheats the incoming pollutant-filled air by recuperating heat from the exiting clean air. As the incoming air passes from one side of the metal tube or plate to the other, heated and cleaned air from the combustion chamber passes on the other side of the tube or plate and heat is transferred to the incoming air through the process of conduction using the metal as the medium of heat transfer. The heat exchanger reduces fuel use but this technology is not as fuel efficient as an RTO or a catalytic oxidizer.
Catalytic Oxidizers (CATOX)
A Catalytic Recuperative Oxidizer (often called a catalytic oxidizer) destroys pollutants like Hazardous Air Pollutants (HAPs), Volatile Organic Compounds (VOCs), and odorous emissions that are often discharged during industrial processes. Catalytic oxidation works similar to a thermal oxidizer- VOC hydrocarbon molecules are broken apart at high temperature. But a catalytic oxidizer uses a catalyst integral to the system, which allows the VOC oxidation to occur at a low temperature (usually 600-700F).
Catalytic oxidizers achieve high VOC destruction efficiency by heating and maintaining a polluted airstream at temperature for a set “dwell” time as it passes through the catalyst. The lower operating temperature results in much lower fuel use than thermal recuperative oxidizers. VOC destruction efficiency can reach 99+%. Catalytic oxidizers can operate with an integral heat exchanger for fuel savings, or without a heat exchanger for capital cost savings.
Kono Kogs: 25+ Years of Experience with Industrial VOC Abatement Systems
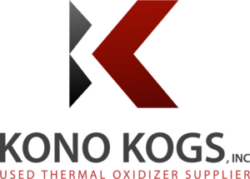
Benefits of working with Kono Kogs:
- 24 Hour customer service and support (phone: 920-615-8804)
- Multiple OEM & technology offerings ensure unbiased recommendations
- Complete aftermarket sales department
- Management with a combined 150 years of oxidizer manufacturing and service experience
Alstom RTO Treating Flexographic Printing Emissions
Case Study: Kono Kogs refurbished & installed an Alstom RTO for a growing flexographic printer. Low cost, proven performance, repeat customer!
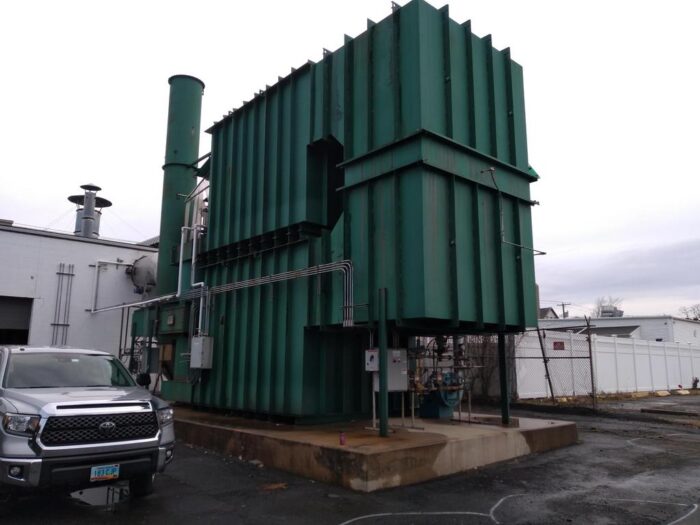
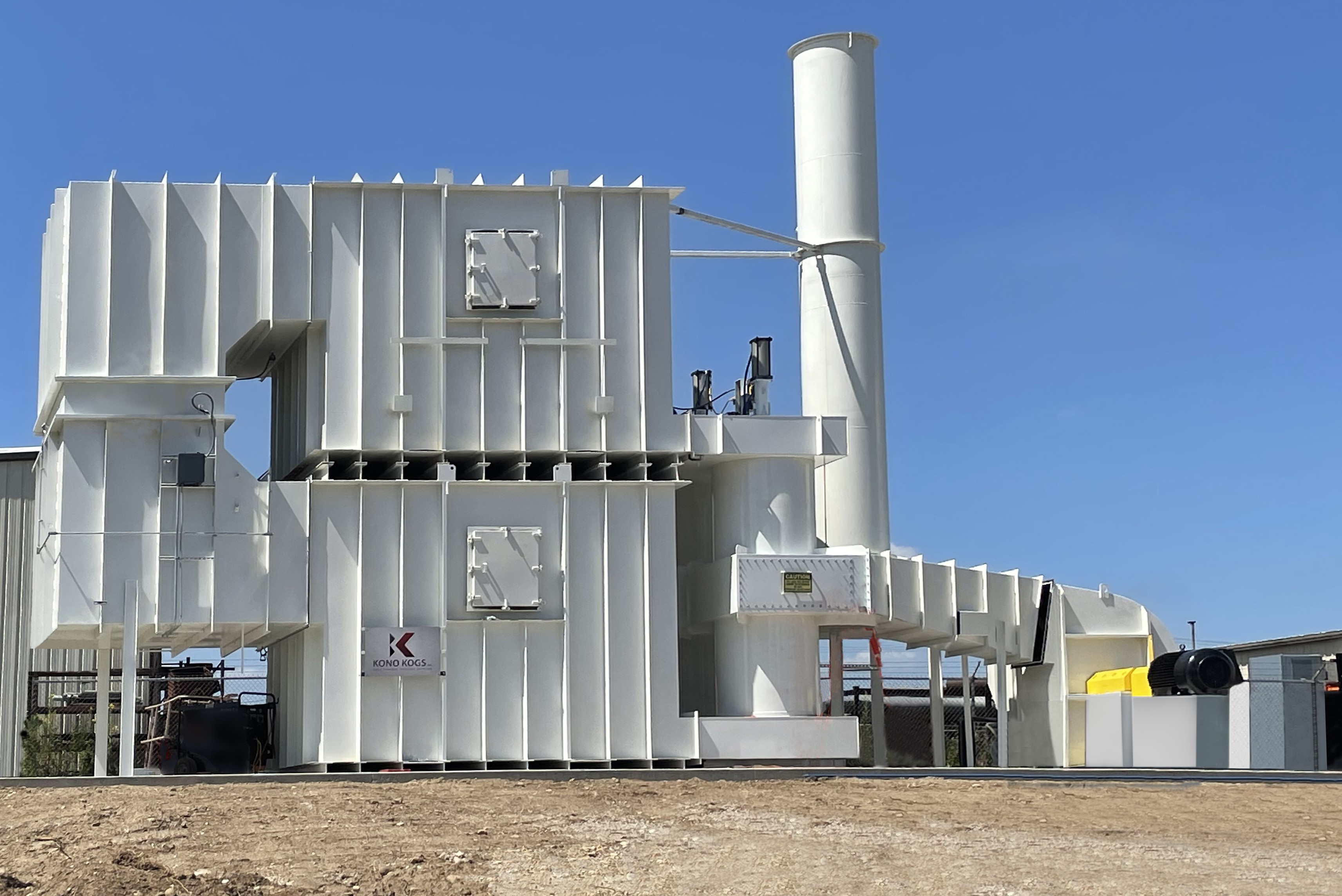