Types of Catalytic Oxidizers
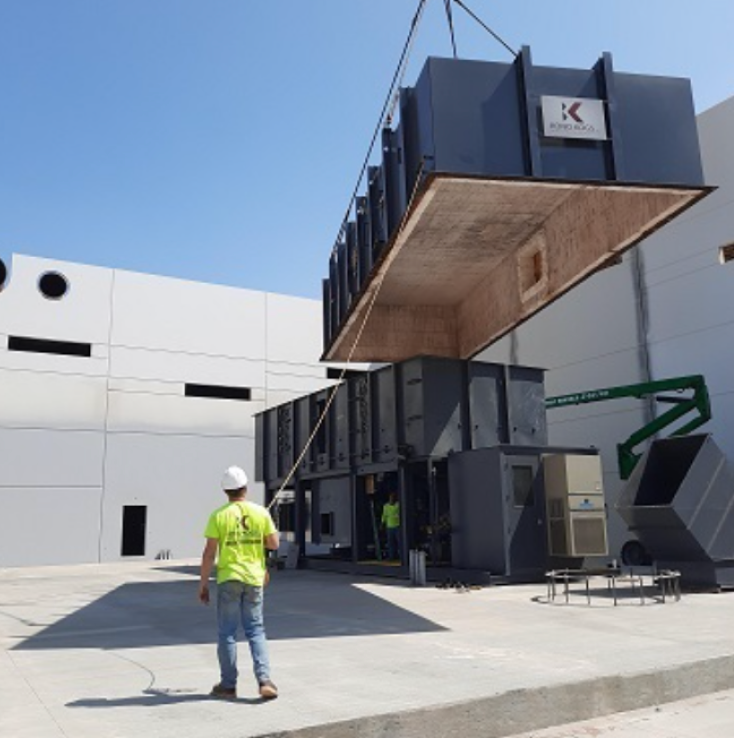
Discover the three types of catalytic oxidizers and their catalyst options.
Learn about the different types of catalytic oxidizers, including direct, recuperative, and regenerative, as well as, common types of catalyst substrates.
Types of Catalytic Oxidizers
Catalytic oxidizers have been a reliable air pollution control technology for decades. The benefit they offer is reduced fuel costs compared to thermal oxidizer technologies. The presence of catalyst in an oxidizer facilitates the oxidation of the volatile organic compounds (VOCs) and hazardous air pollutants (HAPs) at much lower temperatures than thermal oxidizer technology. They typically achieve VOC destruction of 95-98%.
A system's catalyst typically consists of precious metals such as platinum or palladium. Due to the cost of the precious metal content, it's important to apply catalytic systems wisely, ensuring catalyst contaminants are not present in the airstream.
Direct Catalytic Oxidizers
Direct catalytic oxidizers are the simplest catalytic systems available. These systems consist of a fan, burner and a catalyst bed, with simple airflow and temperature control loops. This type does not incorporate heat recovery. They are ideal systems for batch applications with low annual operating hours. Direct catalytic oxidizers can also be a good match for low airflow applications where operating fuel use is low and not a significant cost concern. These systems are the lowest capital cost catalytic design available, due to their relative simplicity. However, this type has the highest operating cost of all oxidizer technologies, excluding direct fired thermal oxidizers (DFTO).
Get more information on catalytic oxidizers.
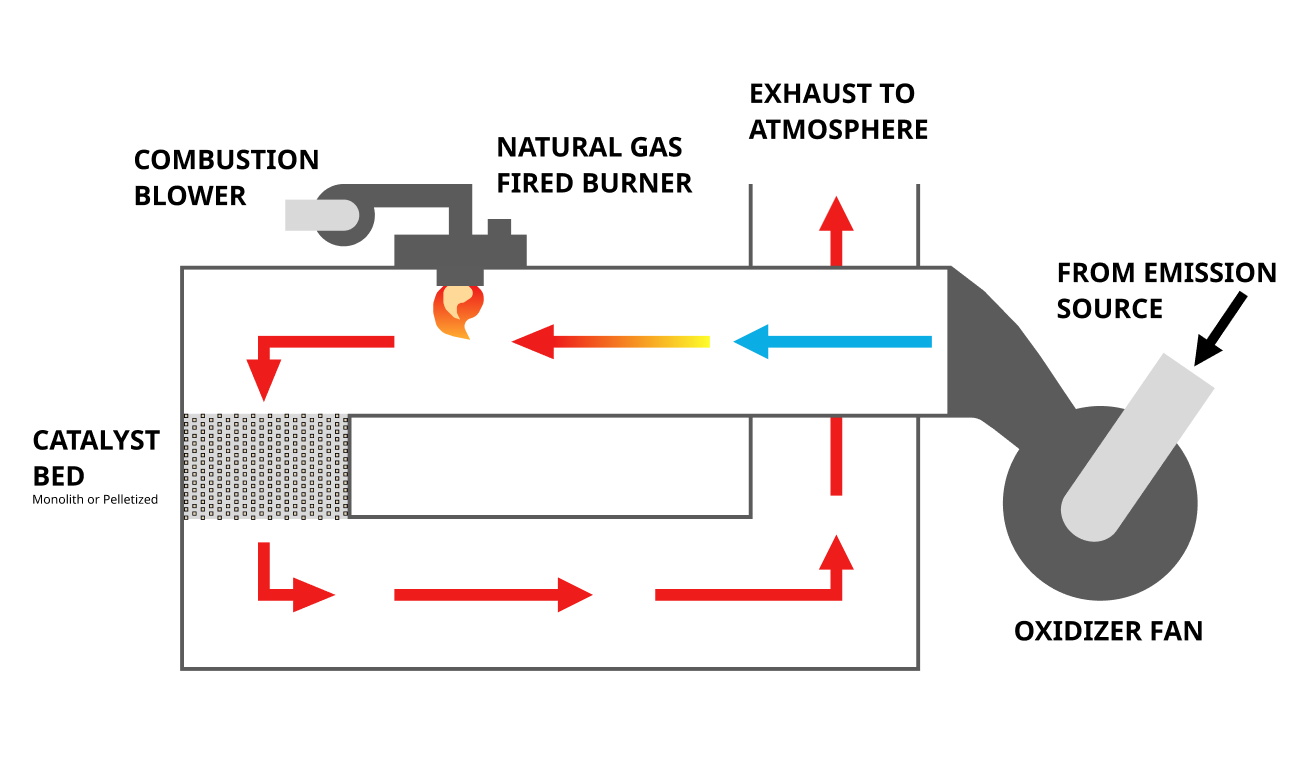
Recuperative Catalytic Oxidizers
Recuperative catalytic oxidizers are very similar to a direct catalytic system. The major difference is the addition of a heat exchanger to capture heat from the outgoing exhaust airstream. The heat exchanger significantly improves energy efficiency and reduces operating costs. It has a much lower operating cost than both a direct catalytic oxidizer or a thermal oxidizer (TOX). However it has higher operating costs than an RTO or an RCO. These systems can be an excellent match for processes such as industrial bakeries and pharmaceutical manufacturing. The heat exchanger can be either an air-to-air type or a more complex design depending on the specific application. Capital cost of these systems is higher than direct catalytic oxidizers, but is comparable to RTO systems, and is lower than RCO systems.
Get more information on catalytic oxidizers.
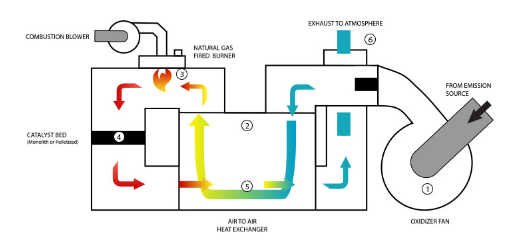
Regenerative Catalytic Oxidizers
Regenerative catalytic oxidizers (RCOs) introduce catalyst into the system to achieve exceptionally low operating costs. Typically, the catalyst is coated onto a portion of the ceramic media in the RTO bed. As polluted air passes over the catalyst the VOCs and HAPs are oxidized. RCOs operate at 750-850 F, much lower than standard regenerative thermal oxidizers (RTO). The regenerative heat exchange principle in these systems combined with the low operating temperature makes the RCO the lowest operating cost oxidizer available. RCOs are ideal for applications with high airflow rates and low VOC concentrations, offering up to 95% thermal heat recovery and 98+% VOC destruction. While they have the highest capital cost of the catalytic oxidizer types, they are by far the lowest operating cost catalytic design available; lower even than an regenerative thermal oxidizer (RTO).
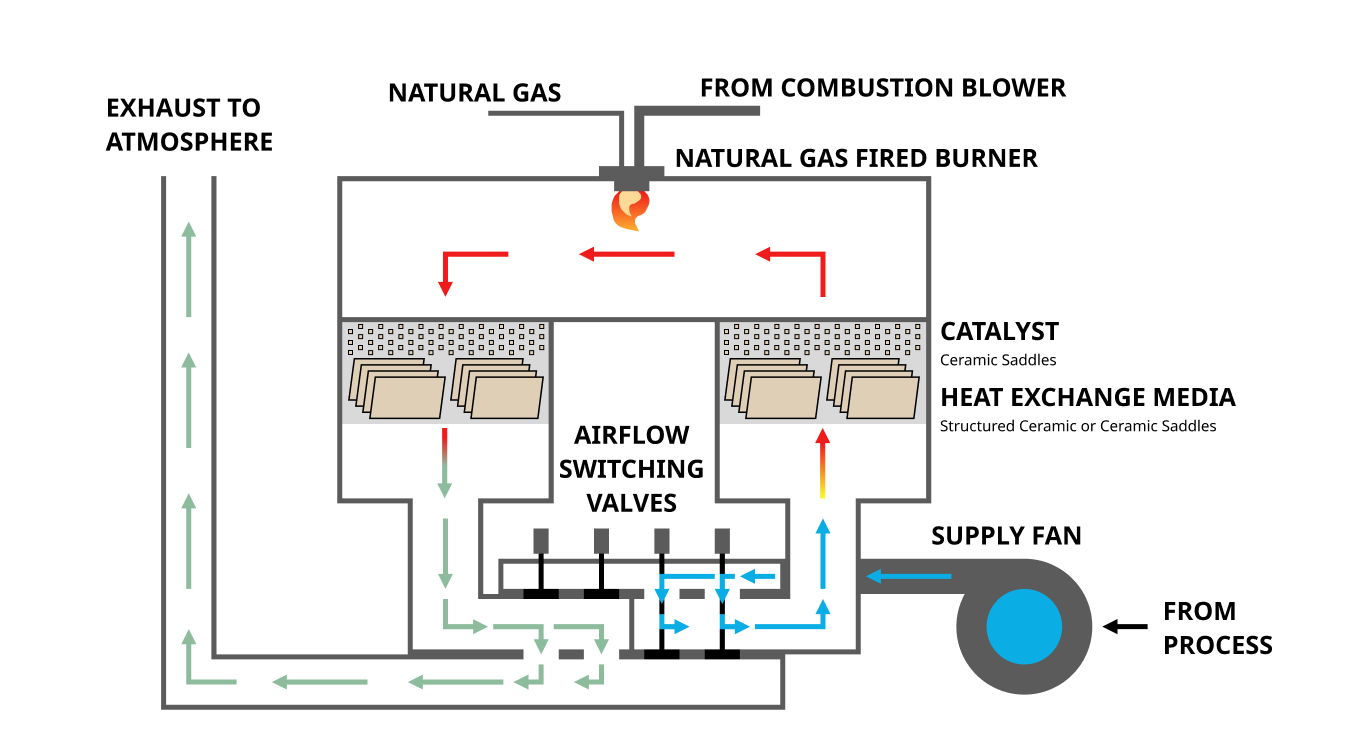
Types of Catalyst Substrates
Catalyst material is typically platinum or palladium or other precious metal. In an oxidizer, the catalyst is always embedded or coated onto a substrate. The substrate is mounted in the oxidizer and the airstream is forced over or through the substrate, mixing the polluted air with the substrate and the embedded catalyst material. The common substrate materials are discussed below.
Note: Some catalyst material is base metal and are homogenous, not requiring a substrate. These are less common in catalytic oxidizers, so they are not addressed here.
Bead Type Catalysts
Bead type catalysts consist of small, spherical beads. Catalyst material (platinum/palladium) is dispersed on the bead. These beads are typically made from ceramic materials or alumina. These beads are contained in a bed and the polluted air is passed through the bed of catalyst. As the polluted air passes over the catalyst at high temperature, the VOCs and HAPs oxidize to water vapor (H2O) and carbon dioxide (CO2).
Bead substrates have the advantage of significantly higher surface area compared to monolith substrates. This makes them 10X-20X less susceptible to contamination of the catalyst by poisons (halogens) or masking agents (silicone, phosphorus). The high surface area of the beads allows for efficient contact between the pollutants and the catalyst, making them suitable for various industrial applications, including bakery emissions, pharmaceutical processing, and chemical processing.
Monolith Catalysts
Monolith catalysts feature a honeycomb substrate made from ceramic or metal. This design allows for a high surface area and low pressure drop, making them effective for high-flow applications. The honeycomb structure is coated with a catalyst, usually platinum, palladium, or rhodium, which facilitates the oxidation of pollutants. Monolith catalysts are commonly used in applications with low-to-no poison or masking agents in the airstream.
Ceramic Media Catalysts
Ceramic media catalyst material is an engineered shape of ceramic with catalyst dispersed on its surface. This type is common in a regenerative catalytic oxidizer (RCO) system. The ceramic substrate also acts as a heat sink in the RCO system. As regenerative systems change airflow direction every few minutes (see the polluted air passes over the catalyst-coated ceramic media and is oxidized to water vapor (H2O) and carbon dioxide (CO2).
.png)
Need help determining if your application is a match for catalytic technology? Contact our expert team.... we would be glad to help!
Catalytic Oxidizer Treating Flexographic Printing Emissions
Case study: See how Kono Kogs helped a first-time buyer of emission control equipment to find and install the lowest total cost of ownership technology for their rapidly growing label printing application
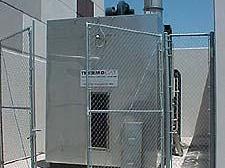